Malcolm Adam and David Coul, Omega Completion Technology
A command-activated sandface valve (CA-SFV) was developed that has significantly improved productivity by enabling improved wellbore cleanup, particularly in high-angle and openhole completions. The sandface valve technology has now seen 35 installations in BP’s Clair Field with a functional 100% success rate. The valve development was taken from concept to installation in five months, including operator engineering reviews.
The sandface valve was developed to meet BP’s requirement for more time control when selectively cleaning up/flowing the reservoir sections. The key objectives of the valve were to allow sequential cleanup of the reservoir section from toe to heel without intervention or incremental rig time. The valve would be activated by a pressure recognition signal; it also needed to deliver the functionality of a sliding side door for future water shutoff capability along the wellbore. The valve design combines a field-proven timer activation mechanism, a transducer and conventional sliding sleeve technology. The resulting tool is the basis for a new completion technique that has application in high-angle wells in a wide variety of oilfield applications.
WELL OVERVIEW
Earlier wells at Clair Field were completed openhole with pre-drilled liner installed across the lower producing zone. The upper two producing zones were isolated by openhole packers and contain two sliding side doors (SSDs) run open to enable production and to provide future water shutoff options. The liner is installed across the entire reservoir section to facilitate openhole tractor-conveyed production logging. It was identified early on that production from these wells was restricted to small areas. As is commonly seen in high-angle wells, the highest drawdown is at the heel section (the source of the main flow contribution). Improvements in well startup would improve production. More importantly, they would ensure access to reserves in areas of the field targeted by the wells, but that were unswept due to the non-productive section of the wellbore.
The sandface valve is operated without intervention and has a one-shot opening function. It also has the future capacity for mechanical opening and closing. Early wells incorporated timer-activated sandface valves only. More flexibility regarding when this valve was to open and allow cleanup was required by the operator. To activate the new valve, a pressure signal that it has been programed to recognize is sent to the valve. To allow this pressure signal to work, the well has to be closed off. This was achieved by pressuring up against the electronic liner shoe (ELS) run at the bottom of the completion string. The ELS was designed in conjunction with the sandface valve. The ELS is run in the open position, providing liner running circulation. It is programed to start a timer countdown to close once it sees the programed hydrostatic well pressure. The valves are programed to open with a staggered opening time. The well would be brought online from the toe section and allowed a period of cleanup. After another pre-programed time, the lower SFVs would open, enabling this middle zone to clean up. After an additional time period, the upper SFVs would open, enabling cleanup of the upper zone and full production from the wellbore.
VALVE DEVELOPMENT
The requirement for the CA-SFV development was driven by three factors—the unreliability of gauging well start-up times and, therefore, difficulty in setting the SFV timer; the need for a design that could eliminate the use of a completion barrier valve (this would mean that the SFV needed to be functioned open on a unique command from surface); the need to eliminate the downhole barrier valve, so the lower completion and cased-hole wellbore cleanout could be conducted in a single trip, saving one to two days rig time per well.
Objectives of the sandface valve included: open on command, availability of a contingency mechanical opening method, a proven reliable primary opening method for remote opening, a proven reliable design for long-term production, and the ability to mechanically open and close the valve throughout the well life.
Two valve designs were excluded during the initial well design screening: control line operated valves, due to the two-stage completion design, and valves operated by surface-applied pressure. The latter was excluded because the well will have been producing at the time of valve opening; therefore, formation will be open.
VALVE DESIGN
The sandface valve design comprises three main sections: the electronic section, the actuator and the SSD. The timer section comprises two independent sets of electronics that provide actuation for the device. Two independent electronic sections provide 100% backup functionality within the valve. The valve is programed prior to installation at surface using simple computer software. Flexibility exists to allow the user to determine the pressure recognition setting for the valve.
The electronics are coupled to the actuator; when activated, they initiate the opening of an internal port in the valve, allowing well pressure to drive the piston and move the SSD sleeve section to the open position. The actuator is a one-shot component. The SSD section houses the valve flow ports. Once actuated, the SSD is decoupled from the piston section of the valve and reverts to a stand-alone SSD; any further functioning of the sleeve requires mechanical intervention. Valve specifications are shown in Table 1.
TABLE 1. Cost-effective solutions to enhance SCR performance for deepwater field development |
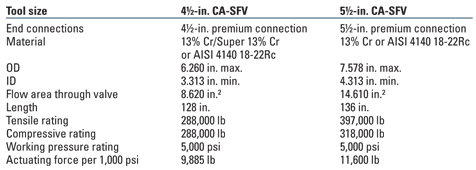 |
FIELD TRIAL A
A field trial installation was conducted in January 2009. This was a two-trip completion design, which would be run openhole and open ended. Standard sandface valves and CA-SFVs were installed in each zone in the lower completion. All valves were installed in the closed position.
Swell packers were used in the openhole section to isolate the production zones. An ELS was run at the bottom end of the completion string in the open position to allow wash-down of the liner. This liner shoe was designed in tandem with the CA-SFV. Once at depth, the liner hanger was set and tested and the ELS was activated to close, making the liner a closed system; then, successful pressure testing of the liner was conducted. Once these operations were complete, the lower set of CA-SFVs were successfully opened on command, enabling well cleanup to commence. The second sets of CA-SFVs were activated by the same command but set to open on a different time delay. The final two zones had standard time-delay SFVs installed and opened as predicted based on the programed timing. The opening sequence for the well is shown in Fig. 1. The staged cleanup of this well was successful. The new completion design has potentially eliminated all contingency milling requirements for the lower completion barrier valve. Cased-hole cleanup had previously required a separate trip; this new completion design saves one to two days rig time over the conventional design.
|
Fig. 1. Wellbore cleanup sequence.
|
|
FIELD TRIALS B AND C
Two further field trials using a combination of command-activated and timer-activated sandface valves have been installed with a 100% success rate.
CONCLUSIONS
A command-activated sandface valve was designed in response to an operator’s need for a remotely operated valve that would allow selective cleanup and production from its multizone completions and would also offer added control over purely timer-based valves that were already being used. The solution to a common oilfield problem of bad well cleanup had to be made less complex and more cost-efficient than conventional solutions or new technology. The key objectives for the equipment were to allow control of when the valve would function open and to improve wellbore cleanup, leading to improved production and reserves access. The timer- and command-activated valves have bridged a gap between complex and costly smart well completions and conventional well techniques. This technology can be transferred to many high-angle completions with production conformance or well cleanup problems.
Perceived benefits in running with this design include the ability to selectively start up the well remotely, without intervention and complicated cleanup/technology has been achieved. In addition, the second-generation command-activated equipment provides more flexibility for future applications, and the technology has enabled secondary improvements to well design and reduced completion operation time.
|
THE AUTHORS
|
 |
Malcolm Adam has worked in the oil and gas industry for 23 years and is Business Development Manager for Omega Completion Technology, where he is responsible for sales and operations worldwide. Mr. Adam began his career at Otis Montrose and moved to Petroline Wellsystems, later acquired by Weatherford.
|
|
|
David Coul joined Omega from Weatherford Asia Pacific, where he held the role of Flow Control Area Manager, based in Kuala Lumpur, Malaysia. He joined Weatherford Petroline, where he was a Heavy Duty Fishing Specialist. He gained initial field experience with Halliburton; prior to this he worked as a Wireline Supervisor in the UK.
|
|