Driving MPD adoption with performance-enhancing technologies
The challenges inherent in drilling for oil and gas are daunting, none more so than uncertain downhole pressure conditions. Managed pressure drilling (MPD), as defined by the International Association of Drilling Contractors, is an adaptive drilling process used to precisely control the annular pressure profile throughout the wellbore. Many technologies and methods have been developed and refined over the past five decades to mitigate and overcome the unique challenges associated with pressure uncertainties. Ever since introducing the world’s first rotating control device (RCD) in 1968, Weatherford has been a pioneer in this part of the industry.
As an MPD industry leader, Weatherford develops innovative solutions and technologies to expand the scope and applications of managed pressure. But managing pressure is not simply controlling the annular pressure profile. It must take into account the myriad of specific operational conditions, formation difficulties, and varying location challenges across the globe. Drawing on the deep knowledge gained by decades of experience, the company’s experts realized an engineered approach to managing pressure would best address the diverse challenges rather than a universal system for any applications. With this philosophy as a guiding principle, different tiers of MPD technologies were developed to address the various operational needs of operators, no matter the challenging conditions or environments.
Creating a closed-loop system with RCD. Rotating control devices provide safety assurance and flow diversion while serving as the entry-point technology for MPD. Originally developed in the 1960s, RCDs were strictly designed for land-based applications, where they were used for flow diversion above a blowout preventer (BOP) to create a closed-loop circulation system. The company’s continuous drive to innovate and improve RCD technology resulted in decades of field-proven success.
MPD applications expanded to places where higher requirements are demanded from the current MPD systems, to address new challenges and environmental conditions. This resulted in the improvement of RCD technology with the introduction of higher pressure and temperature ratings and even American Petroleum Institute qualifications for use in pure-gas conditions. One such example is our polyurethane-based high-temperature sealing element, which increases the temperature rating by 60% over existing polyurethane elements.
As the energy industry matured and grew to the offshore market, Weatherford created new models of RCDs to address the unique challenges of the marine environment, both shallow water and deepwater. Shallow-water rigs use RCDs above the surface BOPs, while deepwater applications involving dynamically positioned drilling vessels typically install RCDs below the tension ring as part of the riser package. Regardless of the application or environment, the RCD is a key piece of technology, enabling operations to maintain a constant annular pressure, create pressure-tight barriers against drilling hazards, and manage inflow from formations.
Adding a choke to better manage pressure. While the RCD diverts fluid returns, the ability to actively manage the downhole pressure profile in the wellbore is performed by downstream surface equipment, specifically a choke. Combining this equipment with an RCD enables MPD techniques, providing greater surface pressure control and management. Weatherford developed the PressurePro Managed Pressure Solution to work in tandem with RCDs to mitigate downhole pressure incidents while improving drilling capabilities.
This system uses a single human-machine interface (HMI) to control the choke. Displayed on a laptop in the driller’s cabin (“doghouse”) or on the rig floor, the HMI enables field personnel to control the choke virtually rather than manually while monitoring important drilling parameters. The operator inputs the pressure set point, and then the PressurePro system automatically maintains it by manipulating the applied surface backpressure (SBP). The choke self-adjusts automatically and instantaneously to variances in downhole pressure for quick, reliable system corrections.
Automating responses to mitigate drilling risks. The Victus Intelligent MPD solution is Weatherford’s premier MPD offering and stands as one of the most advanced MPD technologies in the market. This technology builds on the company’s established RCDs and choke equipment and takes accuracy, control, and automation to unprecedented levels. It precisely maintains bottomhole pressure by integrating rig equipment for machine-to-machine communication, real-time analysis of downhole conditions, and rapid automated responses from a central location.
On the equipment side, the Victus solution adds accurate flow and density measurement through the addition of a Coriolis mass flowmeter, and up to four chokes on a manifold with independent control. An advanced hydraulics model precisely determines real-time bottomhole pressure by considering the effects of fluid and formation temperature, fluid compressibility, and wellbore cuttings. Artificial intelligence (AI)-enabled control algorithms identify well anomalies, alert the driller and MPD operator, and automatically send corrective commands to MPD surface equipment. This enables real-time detection of wellbore influx/losses, and the appropriate adjustments to the equipment can be made based on the hydraulic modeling and intelligent control without operator inputs. The programmable logic controller (PLC)-based system easily integrates anywhere on the rig to provide a reliable, secure MPD infrastructure.
A simplified user interface helps enable users to stay focused on critical parameters and sends alerts on unexpected events. Condition-based monitoring tracks MPD equipment performance and enables proactive maintenance. Reliable automated reporting, such as daily summaries or post-job analyses, further optimizes drilling performance. In deepwater operations, remote control via a single user interface enables robotic riser installation, complete annular isolation device (AID) shutoff, RCD latching and unlatching, and flow routing. Data consistency spans from well planning to real-time operations and post-job reporting. The real-time viewing and engineering evaluation/planning aspects are managed with the CENTRO Well Construction Optimization Platform.
Current developments include improved flow measurements with a high-pressure flowmeter (installed on the standpipe) replacing simple pump stroke counters. Using this new technology provides fluid rheology and mass flowrate properties on the inlet side of the closed-loop drilling circuit to compare with the outflow measurements. This system features better hydraulic modeling with real-time data when compared against the conventional methods of manual mud checks that are updated with far less frequency.
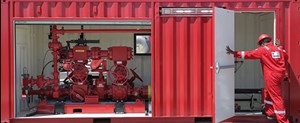
Providing simple, precise pressure management and data capture. PressurePro and Victus technologies are solutions developed for the entry and advanced levels of managed pressure applications. Weatherford identified additional applications that would be best suited to a solution between these tiers. Filling this gap is the company’s newest system, the Modus Managed Pressure Wells Solution, Fig. 1. This system was designed for use in a wide array of applications, in hot or cold environments, and for both land and shallow-water applications. The goal with this system is simple: focus on performance benefits of managed pressure techniques, so that operators can drill more effectively with fewer pressure-related issues.
The Modus solution uses a modular approach to allow for flexible and efficient installation. The system incorporates three equipment skids contained within one sea container, needing only a single lift when unloading at location. The individual skids can be removed from the shipping container for specific placement around the wellsite if required.
The choke manifold arrives in one skid, but the system is configurable to suit each rig-specific requirement, if the chokes need to be placed within existing infrastructure. With two digitally controlled chokes, the system has the flexibility of using either choke independently for isolation or in combination for higher flowrates. Precise control of these chokes enables improved wellbore pressure and equivalent circulating density (ECD) management for more efficient drilling with lighter mud weights. An over-pressure protection system and flow line are integrated into the manifold.
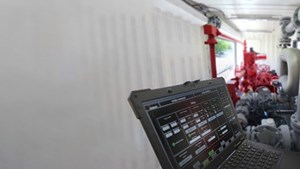
The flow measurement equipment arrives in the second skid. This equipment enables the measurement of the return flow and fluid properties with a Coriolis flowmeter, the proven industry standard for accuracy. Using this continuous mass balance data allows the operator to immediately identify downhole pressure changes in the form of flow anomalies. Real-time visibility of condition fluctuations empowers fast reactions and adjustments to mitigate pressure issues before they affect operations, Fig. 2.
The digital control system is housed in the third skid, and it manages the data and functions of the measurement and control equipment. This digital platform works through a laptop-based HMI, and the operator can see the measured conditions with historical trending and control the pressure through the digital software. The graphs displayed on-screen instantaneously show trending of the downhole conditions, enabling better decisions and faster reactions based on data. For operating in a constant bottomhole pressure mode, the system features snap pressure functions for use during connection makeups. This allows a single-button activation that automatically adjusts the chokes and generates the desired pressure on the wellbore, maintaining constant downhole pressure without flow. Relevant data are collected, stored for post-job analysis, and can be transferred via a well-site information transfer (WITS) interface and viewed in the CENTRO platform, Fig. 3.
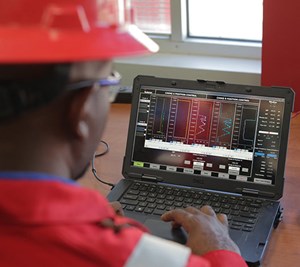
By automating the management of pressure, the Modus solution can react to changes in downhole pressure to protect personnel, wellbores, the environment, and numerous additional assets. As part of an overall well integrity system, the Modus solution enables safe drilling in narrow, shifting, and unknown drilling windows by managing ECD, delivering a trusted approach to improve operational safety and preserve formation integrity.
Demonstrating success in the field. It was Weatherford’s trusted approach earned from more than 50 years of experience, thousands of jobs, and millions of operating hours that drew an operator in Ohio to deploy the Modus solution. Located in the Utica shale, the operator needed to maintain the 8½-in. hole size down to the target depth, to meet authorization for expenditure cost goals.
The Modus solution reduced the time to drill by 60% when compared to the planned well time and allowed the entire section to be drilled in a single run. Key to this operation was the use of MPD techniques to maintain the ideal mud weight and minimize wellbore pressure cycling throughout the lateral section of the drilling plan. The objective was to avoid potential formation damage from heavyweight muds while drilling through formations with uncertain pressure profiles.
Weatherford's technical experts collaborated with the operator during the preliminary planning and engineering stages to capture the scope and set drilling targets for this horizontal well. The teams determined the requirements and created the service quality delivery plan that would not only coordinate the project’s execution and logistics but reduce overall costs. Weatherford engineers recommended the Modus solution as the best option for the operator.
With the plans in place, Weatherford's field personnel performed a rig survey in Ohio, enabling the local team to prepare the footprint and staging area, as well as identify and eliminate potential hazards. At the same time, experts in Texas staged and tested the equipment prior to shipping. The two teams maintained consistent communication with the operator to coordinate delivering the equipment on time. When the Modus MPD solution equipment arrived at the rig site, it was efficiently installed and commissioned for use, and Weatherford’s engineering team quickly adjusted the MPD operations matrix to accommodate a change in the operator’s drilling plan.
Shortly after landing the curve, however, the hole showed signs of a pack-off. After discussions with the operator, Weatherford's MPD team provided options for updated MPD programs to address the situation. The preferred option was to add back pressure while slowly raising the fluid system by 0.5 ppg (0.06 SG). This enabled the rig to continue drilling without waiting to condition the mud and without significantly weighing up the fluid system. With this adjustment, the drilling continued with the same bottomhole assembly and reached the target depth of the long lateral section in a single trip.
Throughout the operation, the Modus solution actively monitored gains and losses, enabling the operator to use a lighter fluid system and save on barite use for weighting up the fluid system. Complementing the lighter fluid system in the wellbore, the Modus MPD technology actively applied surface backpressure to easily adjust to changing downhole conditions. Conventional methods would have required hours or a day to weight up or lighten the fluid system.
By deploying the Modus solution, the operator reached target depth nine days ahead of the 15-day well plan. Additionally, by using a lighter mud weight of 1.0 ppg (0.12 SG) and adjusting backpressure to compensate for wellbore and formation pressure, the operator reduced overall costs. The Weatherford solution drilled an 18,000-ft (5,486-m) lateral in a single trip, achieving an 18% faster rate of penetration (ROP), as compared to the previous four wells drilled conventionally.
Envisioning the future of MPD wells. This recent case of value generated through performance improvement is just one illustration of the company’s broader strategy for the Modus solution. In 2024, a fleet of systems will be deployed to locations across the globe to further expand the use of managed pressure technologies and enable other operators to understand and achieve the long-term value of delivering higher-quality wells with fewer surprises.
For years, the energy industry has applied managed pressure techniques only on the drilling aspects of the well construction process. Weatherford sees managed pressure differently. It is a performance-enhancing solution for numerous, if not all, well classifications, including horizontal, directional, development, and multi-laterals. By redefining what can be achieved by managing a wellbore’s pressure, other activities—including cementation, tubular and completions running—can benefit from a stable wellbore, avoiding wellbore collapse and formation damage while improving efficiency.
For example, by managing pressure during cementing, operators can more proactively respond to well events, such as gains and losses, improving zonal isolation. Managed pressure cementing is particularly effective in wells with a narrow drilling window, weak formations, or very tight margins. When the tools and techniques developed for managing pressure are applied to completions operations, it is possible to easily manipulate pressure while setting completions components, improving efficiency, and reducing risks during this phase of a well’s lifecycle.
Managing pressure better within a safe operating window can apply to any well and any operation. Now, with the introduction of the Modus solution and more appropriate managed pressure systems for different applications, it is now possible to manage well pressure in a greater number of wells, positioning Weatherford solutions to deliver comprehensive pressure management for fewer surprises and higher-quality wellbores, increased borehole stability, and more productive wells.
- Coiled tubing drilling’s role in the energy transition (March 2024)
- Advancing offshore decarbonization through electrification of FPSOs (March 2024)
- Subsea technology- Corrosion monitoring: From failure to success (February 2024)
- Digital tool kit enhances real-time decision-making to improve drilling efficiency and performance (February 2024)
- E&P outside the U.S. maintains a disciplined pace (February 2024)
- U.S. operators reduce activity as crude prices plunge (February 2024)