|
|
|
By Petroleum Technology Transfer Council |
Polylined tubing reduces downhole failures
Field results in the past few years have proven that using polyliners can increase uptime and save money – even over plastic coatings
Jim Hickman, Western Falcon, Houston, Texas
Many operators are using polylined tubing to reduce well failures from rod-tubing wear and tubing corrosion in artificial lift and injection wells. BP America, ChevronTexaco, Conoco and Fasken Oil and Ranch have used polylined tubulars in over 41 wells with substantial savings in operating costs.
POLYLINER DESCRIPTION
Polyliners, which are mechanically-bonded materials, provide cost savings by allowing the use of lower-quality tubing (blue, green, etc.). This bonding practice allows liners to be installed over used internal plastic coatings without the cost of removing the coating. The end finish process during installation eliminates the need for corrosion barrier rings, inserts, special torque procedures, and/or service technicians.
Polyliners are not a solution to all downhole tubular problems. Material limitations preclude their use in high-pressure gas wells and downhole applications exceeding 210°F. The liner causes a slight reduction in the pipe’s inside diameter. Pumps, rods, and rod boxes should be inspected for sharp edges and heavily pitted areas that can damage the liner. A cursory wellsite inspection of all downhole components should be made to avoid causing mechanical damage to the liner.
FIELD RESULTS
BP America. The Carracas 19-b4 is located in Carracas Canyon, New Mexico, in a National Forest, which limits site access from 6 to 7 months a year. Vastar drilled this highly deviated well in 2000. A beam pump was installed in 2001. The well was never a viable producing asset, because it went down every 6 to 8 days due to rod-on-tubing wear, rod and pump failures. Polylined tubing was installed in April 2002, Fig. 1. The well is currently producing 100 Mcf and 40 bwpd. It has not experienced a tubing or rod-related failure since.
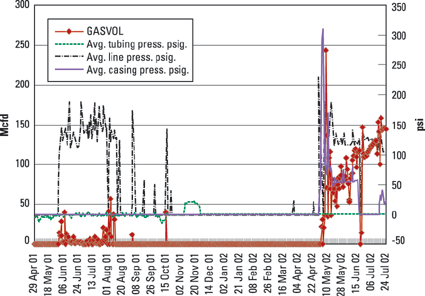 |
Fig. 1. BP America Carracas 19-b4 well performance with polyethylene-lined tubing.
|
|
ChevronTexaco. ChevronTexaco specified 17 wells in McElroy field for an extensive study in rod wear. Production rates vary from 40 to 500 bfpd with a high watercut. Depth of the 17 wells averages between 2,800 and 3,000 ft. Wells exhibit extensive rod-on-tubing wear and corrosion failures. Bare-tubing life averaged 112 days. To improve the situation, the existing tubing was pulled, rod boxes and pumps were inspected for corrosion pitting and sharp edges and then polyliner was installed. Installation dates range from early 1996 through fall 1997, with the exception of one well where the liner was installed in 2001. One well was dropped from the study because it was converted to an injector. At this time, the average lined-tubing life is over 1,800 days, Fig. 2. The reduction in tubing workover failures has substantially reduced operating costs. With a representative workover cost of $4,000 per well, (not including tubing replacement, lost production or associated pulling charges) each well realized about $64,000 in savings. Liners have eliminated an average of 16 workovers per well.
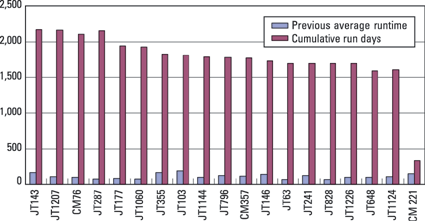 |
Fig. 2. ChevronTexaco. McElroy field wells average days in operation before and after polyliner installation.
|
|
Conoco. Howard/Glascock field was discovered in 1925. Average depths are 3,000 ft with a bottomhole temperature of 130°F. The 375 field wells produce low gas volumes containing a high H2S level. Water volumes vary from 1 to 1,200 bwpd. Bacterial corrosion problems have been associated with the high water cut. Average bare tubing life was 2 years for corrosion/rod failures. Polylined tubing was installed in 17 wells that were taken as a field reference. Liner installations began in October 1995 and continued through early 1998. No tubing failures have been reported as of January 2002, Fig. 3. Cost savings using an average workover cost of $5,000 have been about $157,000 since January 2002.
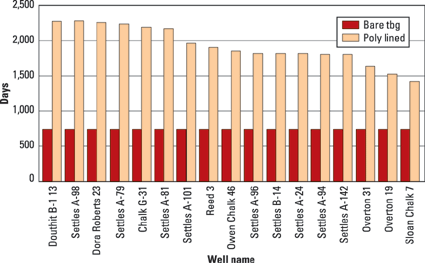 |
Fig. 3. Conoco’s Howard/Glascock field well data as of January 1, 2002.
|
|
Fasken Oil and Ranch, Midland, Texas. Fasken uses polylined tubing for production injection, and disposal wells in 10 fields. Candidate wells were chosen in areas where failures were especially costly. Polyliners were used in both injection and production wells. On average, in these rod-pumped producers, bare tubulars were lasting only 6 to 9 months. Representative examples from various Texas fields illustrating results with polyliners follow.
Phil Wright Sprayberry 204, Midland County, is a 7,700-ft injection well. Internally plastic-coated tubulars developed a leak in April 2000 and again in October 2001. Polyliner was installed over the internal plastic-coated tubing at a cost of $11,935 vs. replacement tubular cost of $38,500.
Rose Creek North 302, Sterling County, is a 4,400-ft injection well. Internally plastic-coated tubulars developed a leak in March 2000, at which time polyliner was installed over the internal plastic-coated tubing at an estimated cost of $7,285 vs. tubular replacement cost of $23,500.
GG Wright 17, Dawson County, is a 7,500-ft injection well. This was a production well that was converted to an injector in December 2000. The production tubing was polylined for an estimated cost of $11,625 vs. tubular replacement cost of $37,500 for new internally plastic-coated tubing.
Rose Creek North 601, Wolfcamp Formation, Sterling County, is a producer that was experiencing rod wear. Polylined tubing was installed in May 2000. Before installing polylined tubing, tubing wear failures occurred every 210 days. No failures have been experienced with lined tubing.
Germania Grayburg 607, Grayburg Formation, Midland County, is a producer that was experiencing rod wear. Polylined tubing was installed in July 2001. Before this, tubing failed once a year. No failures have occurred with lined tubing.
MTS SA 201, San Andres Formation, Dawson County, is a producer that was experiencing rod wear. Polylined tubing was installed May 2001. Before installation, tubing failures occurred every 9 months. No failures have been experienced with lined tubing.
ECONOMICS/LESSONS LEARNED
Polyliners have proven effective in drastically reducing well operating costs associated with rod-on-tubing wear and tubing corrosion failures. There are more than 10 years of successful installations of polylined tubing in the U.S. Polyliners have been installed in over 3,000 wells, solving corrosion and rod-on-tubing wear-related problems while offering power savings. The product has been particularly effective in mitigating rod-on-tubing wear in beam-pumped and progressive cavity-pumped wells. Benefits can be realized in highly deviated and doglegged wells without additional costs for slimhole rod boxes or rod guides. The product has been equally successful in controlling tubular corrosion in other artificially lifted wells and disposal wells. The liner has also proven resistant to wireline, acid, and chemical damage.
ACKNOWLEDGMENT
The author thanks the following individuals who contributed operating data and reviewed the content accuracy of this article: Dan Crosby and Allen Kutch, BP America, Houston; Ed Gibson, ChevronTexaco, Midland; Johnnie Bowerman, Conoco; Calvin Turner, Fasken Oil and Ranch.
THE AUTHOR
|
 |
Jim Hickman, sales manager with Western Falcon in Houston, is responsible for worldwide marketing. He has over 20 years of oil and gas experience, 16 of which were with a major supplier of internal plastic coatings. jimh @westernfalcon.com
|
|
|
|