FPSO technology: Accelerating FPSO performance evolution
The need to accelerate the performance evolution of floating production, storage, and offloading (FPSO) vessels is growing. As the demand for not only FPSO performance but also their quantity increases, there is a growing emphasis on optimizing production throughput, ensuring equipment uptime, and reducing carbon footprint. To achieve these goals, this article proposes open collaboration and digitalization as key drivers of FPSO performance evolution.
Collaborative initiative. The authors introduce an open coalition comprising Rockwell Automation, Sensia, Cognite, and SLB, which brings together expertise in automation, digital technologies, asset performance management and production experience. The coalition aims to integrate digital solutions early and throughout the FPSO life cycle to enhance efficiency, safety and sustainability, enabling comprehensive application within a flexible, expandable architecture.
The floating production, storage, and offloading (FPSO) market continues to grow, as strong demand is forecast to span this decade and beyond. In parallel with this growth, pressure is mounting for these vessels to perform at peak efficiency and the highest level of safety while simultaneously achieving a net reduction in their carbon footprint. However, the industry’s conventional ways of working are challenged in meeting these imperatives across all stages of the project cycle, from design through construction to operations.
For FPSO performance to achieve ambitions and meet expectations over the next decade, overall FPSO operation must evolve beyond the constraints of the closed ecosystems paradigm. Also, implementation of digital solutions has primarily been executed in isolation, not in an integrated manner, thus severely restricting the overall solution effectiveness. The traditional approach that relies heavily on manual workflows has several inherent challenges and flaws, including scalability, solution maintainability, cost-effectiveness, solution life expectancy, and ease of adoption. It is clear that a new approach is called for—one that accelerates the evolution of FPSO performance by introducing open collaboration and powered by digitalization, automation and contextual data and analysis at scale.
Engaging early in open collaboration to advance FPSOs. What is meant by “open” collaboration? Open collaboration has two facets: The first is based on openly connecting any number of expert partner companies to work together to tackle relevant challenges instead of the conventional siloing when problem-solving, Fig. 1. A basic tenet of open collaboration is that the performance of any single component of an FPSO cannot be improved without considering the whole; thus, the collaboration partners must have wide-ranging expertise across subsurface, subsea and topside.
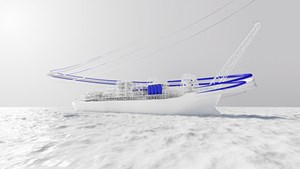
Openness also applies to the digital technological infrastructure that develops through this approach to FPSOs as coherent systems in themselves, not collections of individually digitalized technologies and systems that are patched together as an afterthought. This is inherently an open platform approach, enabling the use of data in multiple contexts, not the current closed, proprietary way. Open collaboration is most effective when it initiates with early engagement, because the potential to impact any subsequent activity across the full FPSO life cycle is still fully available.
Introducing openness early on, whether in the project design, build, or operations phase, accesses the most opportunities for workflow integration. Implementing scalable digitalization and automation is critical to avoid the all-too-common approach of reverse engineering to incorporate these game-changing technologies and workflows. Only this early and open digital approach can give operators better visibility into their operations for increasing reliability and predictability and assuring equipment uptime and performance.
Introducing the FPSO coalition. Leading the evolution to open collaboration and what it can deliver globally for evolving FPSO projects, operations and sustainability is a new coalition comprising Rockwell Automation, Sensia, Cognite, and SLB. As performance integrators with an extensive history in the oil and gas industry that spans the reservoir through production and processing, both onshore and offshore, the coalition’s strength comes from its collective knowledge, expertise, and dedication to open collaboration as the critical accelerator of innovation, digitalization and decarbonization:
- Rockwell Automation is synonymous with automation, primarily for control and safety systems, as well as proficiency in power systems. As the leading OEM module automation supplier in the FPSO industry, Rockwell brings to the coalition proven performance strategies and an advanced digital solution portfolio that includes networking and cybersecurity capabilities.
- Sensia unifies sensing, intelligence and action at oil and gas facilities by combining automation, real-time control, and digital technologies. This original portfolio has expanded with the addition of market-leading technology for metering supervisory systems and measurement to deliver a complete metering package solution.
- Cognite empowers asset-intensive industries with contextualized, trustworthy and accessible data to help drive their full-scale digital transformation. In the context of FPSOs, Cognite enables unifying engineering, information, and operational technologies (ET, IT, and OT) to ensure seamless integration and contextualization of the data that informs production applications.
- SLB drives value creation through the combination of its foundational production expertise in the energy domain, OEM, digitalization, and chemical and process technologies within the context of FPSOs, including complex integration, project management, and asset performance management capabilities.
Because the FPSO has unique requirements for meeting production specifications and achieving maximum throughput—even as field dynamics change over time—the coalition can expand its industry partners, as necessary, for identifying and implementing the most appropriate solutions and services.
Accelerating FPSO performance evolution. Via collaboration, the open coalition enables FPSO stakeholders to shorten the time to first oil and gas, assure equipment performance, optimize FPSO production throughput, and lower carbon footprint at scale. The route to achieving these goals spans three areas of scope: project design, operations, and sustainability. Although design scope is focused primarily on newbuilds, the coalition is available to help any FPSO evolve its performance, whether it’s a new or existing vessel through many activities, such as upgrading equipment or introducing integrated workflows through many activities.
Addressing operational challenges. Each piece of equipment, each system, and each process aboard an FPSO does not exist by itself but is part of the operational ecosystem. That’s why optimization cannot be implemented as a fragmented application but must account for effects of optimization, both up- and downstream of the focal point.
The breadth of expertise integrated by the open coalition enables the coalition to easily take this big picture view that fully integrates all details without any loss of fidelity. This is the essence of asset performance management (APM), Fig. 2. APM knits together data capture, integration, visualization, and analytics capabilities to support improving the reliability and availability of an FPSO and its physical equipment assets and processes across six levels:
- Asset health and reliability: ensure predictable uptime, cost efficiency, and operational security.
- Maintenance management: plan, prepare and execute to prevent or fix breakdowns.
- Site execution: with safety first in mind, and then efficiency in execution.
- Integrity and process safety: assess mechanical integrity and safety risk, such as for integrity and corrosion, process safety criticality, and risk analysis.
- Production integration: looking at the totality of the system and system-level optimization for a holistic approach to improving performance.
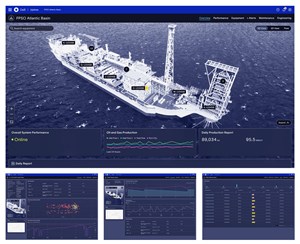
The coalition is advancing APM across the FPSO energy production journey by combining digital twins and an open suite of apps to support continuous monitoring and collaboration, proactively identifying issues and optimization opportunities. A hybrid of data-driven and physics-based models is used to simulate multiple scenarios of solutions that bring together the coalition’s OEM and domain expertise for evolving FPSO performance.
A key enabler of APM is remote and autonomous operations that leverage the latest in robotics, data contextualization, control and automation. In recognition of the large role that automation plays in digital transformation, the coalition is staffed with domain and automation experts to support scalable digital technologies for operating more efficiently across an FPSO’s life cycle. After all, to truly digitalize an FPSO, the foundational architecture and measurement devices must be in place and aligned with robotics and automation to generate the required process data that feed digital applications. In turn, this enables the users and machines to generate actionable insights within the APM through deep dives into analytics and simulation.
The digital integration of automation, including fixed and mobile robots and drones, to FPSOs was investigated by Petrobras in a 2022 OTC paper toward the goal of developing FPSOs as normally unattended facilities (NUFs). As the designer and operator of the largest fleet of floating production units in the world, including FPSOs, Petrobras is keenly interested in advancing operations toward NUFs to reduce work hours exposure to risk and thus limit their HSE risk while also improving sustainability by cutting travel-related carbon emissions. All this would contribute to improving operational (opex) costs.
On the typical 160-person FPSO studied, opex over 25 years may exceed $1 billion, and the total amount of work hours exposed to risk may reach 17 million. Within the constraints of technology gaps, when it comes to human-independent equipment (including collaboration among suppliers) and naval operations automation, Petrobras noted additional considerations: Vessel size may not depend on the size of living quarters so much as hydrocarbon storage requirements, and which of these takes precedence affects capital expenditure cost for the FPSO design and build. Obviously, the coalition’s model of open collaboration among technology and equipment suppliers, and starting design or refurbishment from a reservoir perspective, coordinate and streamline design and implementation validation.
The coalition is implementing robotics through an open, platform-independent solution for remote deployment and control. Although this is done most efficiently in the project design stage, existing FPSOs can be retrofitted to accommodate robotics. This is an obvious path, following the widespread adoption of remotely operated vehicles, which are essentially aquatic drones supporting offshore production and processing operations. Fixed and mobile robots and arial drones excel at performing repetitive tasks in a consistent manner can replace the predominantly manual approach currently on FPSOs, Fig. 3.
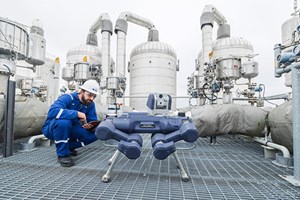
Taking people out of routine monitoring and inspection enables them to address more critical tasks and is also key to improving their safety. One example is removing people from potentially hazardous exposure situations, such as confined spaces where robots and drones can be sent to investigate and thoroughly document visual, thermal, acoustic, and air quality status with their various sensors (payloads). The high-frequency data collected during robot deployments automatically update the FPSO’s digital twin, which in turn is connected to the APM to generate insights.
Improving FPSO sustainability. Automation and remote control are instrumental for improving the safety of personnel on board (POB) by replacing manual tasks, and the new workflows required can also enable minimizing headcount. With reduced POB, numerous benefits to sustainability cascade. The required transport of personnel and supplies is reduced, thus cutting related emissions, as AR/VR is leveraged to conduct troubleshooting and issue resolution remotely. Unplanned downtime can further be reduced through the conditional monitoring that APM and digital twins enable, while they also bring new efficiencies and coordination to planned maintenance activities.
Another obvious source of emissions, besides those related to the transport of personnel and supplies, is flaring. To implement flaring reduction as a component of FPSO emissions management, the coalition helps identify and plan the best path forward in consideration of options, such as diagnosing optimal gas-to-X candidates through conducting technoeconomic analyses and implementing design and delivery of a selected flare abatement option, including full digital integration. As part of improving overall FPSO throughput by identifying and remedying bottlenecks anywhere in the system, the coalition seeks to, as possible, eliminate routine flaring. If any unplanned flaring events occur, the approach is first to minimize damage and then to identify the root causes of the loss of containment for improved control.
Improving FPSO sustainability also can be addressed via enhanced energy management, specifically in reference to the common utilities term WAGES, representing water, air, gas, electricity and steam. The FPSO coalition approaches this subject using a variety of digital applications, all based on the foundational principles of a scalable approach to energy monitoring in the context of maximizing production. Results of utility consumption and trends are illustrated via dashboards, and algorithms provide direction in terms of improvements and optimization. The open architecture within the coalition also provides connectivity to third-party applications that may address specific issues. As with many digital solutions, energy management requires a strong correlation between the application itself and the implementation workflows and consulting services.
One aspect of sustainability for which industry awareness is steadily growing is cybersecurity. Although cybersecurity is implemented to protect data, operations and assets, it is intimately related to sustainability, especially in the unforgiving environments in which FPSOs are stationed, often 200 or more miles from shore. After all, controlling emissions and discharges can be severely compromised by a cyberattack. Unfortunately, the degree to which cybersecurity is in place is typically dependent on the age of the FPSO. That’s why a primary goal of the open coalition is to ensure that all FPSOs, whether newbuild or in operation now, operate with cybersecurity in the fore to identify, assess, manage, mitigate and respond to information security risks.
The coalition is also positioned to address concerns related to the impact and footprint of chemical treatment programs. This initiates with developing a complete understanding of the results that chemical treatment programs bring for the FPSO, Fig. 4. The current chemical management paradigm is largely based on the assumption that a single, simplistic set of dosing instructions should cover a large variety of process conditions. However, in most cases, the injected chemicals are either over or underdosed. To address this situation, the coalition essentially proposes to do more with less chemicals, by making sure that the chemicals are injected at the right time and in the right quantity to address the target challenge. Novel multifunctional chemistries and advanced process controls can be further unlocked through digital workflows and technologies, all while ensuring that asset health is managed in accordance with company policies.
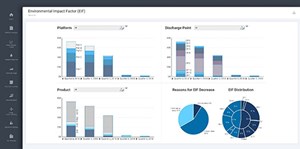
Conclusions. It’s an all-too-obvious analogy to compare implementing improvements in the conservative offshore industry to turning a big ship—it’s a slow, step-by-step process. But digital doesn’t wait, which is why the coalition of SLB, Rockwell Automation, Sensia, and Cognite is open to collaboration with any and all FPSO players and to using the most appropriate technology instead of limiting selection to a closed catalog, particularly in regard to digital ecosystems. That didn’t work well in the past, and the stakes are higher now.
Instead of implementation of digitalization as a sequential process of point solutions, FPSOs require a true performance evolution of comprehensive solutions within a flexible, expandable architecture. And we believe it is the breadth of integration and expertise offered by our unique coalition that is the key enabler for bringing together two established, well-known companies that have supported the industry for more than 100 years—particularly for domain and OEM expertise, chemistry, process technologies, automation and control, safety, and power—and two relatively new companies born of the digital age and positioned to bring digital and data solutions across measurement, intelligent action, and data contextualization to fruition quickly and enterprise-wide. The open FPSO coalition is the catalyst to not only kick-start but sustain accelerated FPSO performance evolution. We invite you to join us.
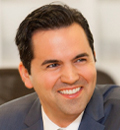
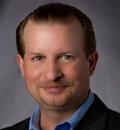
- Advancing offshore decarbonization through electrification of FPSOs (March 2024)
- Digital transformation/Late-life optimization: Harnessing data-driven strategies for late-life optimization (March 2024)
- The reserves replacement dilemma: Can intelligent digital technologies fill the supply gap? (March 2024)
- Subsea technology- Corrosion monitoring: From failure to success (February 2024)
- Digital tool kit enhances real-time decision-making to improve drilling efficiency and performance (February 2024)
- Digital transformation: Digital twins help to make the invisible, visible in Indonesia’s energy industry (January 2024)
- Applying ultra-deep LWD resistivity technology successfully in a SAGD operation (May 2019)
- Adoption of wireless intelligent completions advances (May 2019)
- Majors double down as takeaway crunch eases (April 2019)
- What’s new in well logging and formation evaluation (April 2019)
- Qualification of a 20,000-psi subsea BOP: A collaborative approach (February 2019)
- ConocoPhillips’ Greg Leveille sees rapid trajectory of technical advancement continuing (February 2019)