Tackling methane emissions: It’s time to act
The oil and gas industry’s methane emissions are a big problem for it, and for the world. To minimize the impact of oil and gas development on climate change, this problem needs to be addressed by the industry head on—and urgently.
A potent greenhouse gas (GHG) responsible for approximately 25% of anthropogenic global warming, methane drives near-term climate change. Its effect is 84 times greater than CO2 over a 20-year period, and that outsize influence lingers. Over a century, one ton of methane has the same effect as 28 tons of CO2.
Scientists and policymakers are now prioritizing methane reduction, and the energy industry is a prime target. In 2020, oil and gas operations globally emitted close to 80 million tons of methane—over one-fifth of all methane emissions from human activity.1, 2 (IEA, 2021; Jackson, et al., 2020).
Moving now to reduce methane emissions will deliver benefits that just aren’t possible by reducing carbon dioxide. Simply put: it’s the fastest way to slow the current rate of global warming. It’s also the industry’s duty to act.
Doing the minimum on methane may make economic sense in the short term; however, in the long term, environmental and social issues will catch up, and having done the minimum will be economically disadvantageous. The social cost of emitted gas is typically 10 times higher than the market price and thus far, those costs have largely been externalized. It won’t stay that way amid growing social consciousness around climate-related issues and dynamic government policies.
REGULATION FOR METHANE REDUCTION
Aiming for a 45% reduction in 2012 oil and gas methane emissions by 2025, Canada started applying stricter mitigation rules in 2020. New facility-wide venting limits and pneumatic equipment standards take effect in 2023.
The UK Oil and Gas Authority tightened flaring and venting guidance in 2021, requiring zero routine flaring and venting for all operators by 2030 “at the latest.” Norway has banned non-emergency flaring since 1972 and has taxed all offshore hydrocarbon combustion since 1991.
In the U.S., methane reduction rules are being reinstated, while the EPA’s latest ambitious regulation aims to reduce methane emissions from oil and gas by 70%. Additional U.S. legislation proposes punitive charges for natural gas venting.
Customers and investors are also applying pressure. In 2021, 168 investors, managing over $6.23 trillion in oil and gas assets, signed a statement backing the need for methane reduction rules and called for more stringent EPA regulations.
Today, the industry is moving in the right direction. BP and Shell were two of the earliest firms to peg executive compensation to climate action; many of their peers have since followed. “Twelve companies participating in the Oil and Gas Climate Initiative (OGCI) have committed to aiming for zero methane emissions from oil and gas operations by 2030, with other IOCs and NOCs committing to reducing GHG emissions and routine flaring.
SETTING A STRATEGY FOR METHANE MITIGATION
The good news is that methane reduction is actually an opportunity for the energy industry. Methane may make up 57% of oilfield emissions, but it’s the easiest to mitigate.3 (Beck, et al., 2020).
Globally, oil and gas can reduce its methane emissions by 70%, using today’s technologies, according to the International Energy Agency (IEA). Around 40% can be cut at no net cost, because the value of the captured gas is higher than the cost of abatement.
The energy industry’s methane emissions arise from two main sources: leaks and vents. Leaks, also referred to as fugitive emissions, come from unintended events like holed pipelines or leaking seals. Vents are deliberate emissions, whether from equipment actuated by natural gas or maintenance activities.
A small number of “super-emitter” leaks—like open thief hatches, unlit flare stacks or open bypass valves—create a disproportionate amount of upstream oil and gas methane emissions. The highest-emitting 5% are responsible for approximately 50% of emissions.4 (Brandt, et al., 2016).
So, it’s often better to find, then fix. Surveying and detecting leaks, then measuring both leaks and vents, captures their true extent and helps target remediation efforts precisely. This systematic approach is much more effective, because it identifies the major leaks—the super-emitters—and provides hard data to help prioritize in-field equipment replacement, Fig. 1.
Standard operating procedures (SOPs) must also change to help meet the new emissions goals, and that has many consequences. For example, if simply venting gas prior to compressor maintenance is no longer allowed, what new equipment will be needed to cope and where? Which is the best option for each application? Is it suitable for remote sites?
A holistic approach is needed that spans all activities: detection, measurement, quantification, prioritization, action and ongoing monitoring. The rest of this article covers some of the available and emerging methane reduction technology, the current gaps and the role of digital.
FINDING METHANE EMISSIONS
Documented equipment that vents can be relatively easy to identify, while larger production facilities often already have sensors in place to monitor fugitive methane and other emissions. However, a major technical challenge is cost-effectively locating undocumented upstream and midstream vents or leak sources, particularly where there are large numbers of well pads in remote, unmanned locations.
Traditional upstream leak detection—employing handheld detectors or optical gas imaging (OGI) cameras—can identify individual leak sources, but it is an inefficient way to screen a large number of facilities to identify a small number of super-emitters. Instead, mobile systems mounted on satellites, airplanes and drones can effectively locate super-emitting needles in a haystack of low-emitting sites, Fig. 2. These systems generally trade frequency for sensitivity, with close-by sensors providing the most sensitive measurements and far away sensors scanning the most sites per day.
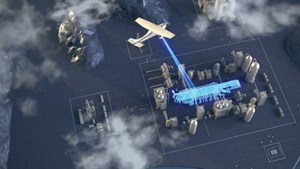
Tiered inspections, which use broad surveys of large areas to direct subsequent, more precise surveys only where needed, can deliver highly efficient monitoring by leveraging many new technologies. For example, airplane surveys of large areas followed by handheld OGI inspection only on sites prioritized by the airplane may result in equivalent emissions reduction at up to six-times-lower cost than the traditional approach of unguided OGI surveys.5 (Rashid, et al., 2020).
Despite these advantages, mobile monitors provide only a snapshot of emissions, which may be insufficient when emissions are intermittent. Continuous monitors address those emissions by providing near 24/7 site monitoring. Many styles of continuous monitors are being developed. For example, positioning multiple IoT-enabled sensors on a well pad perimeter can detect airborne methane, triangulate to the leak location, quantify the emission rate and alert the operator, Fig. 3. If the sensor is accurate enough, a single optimally located sensor can suffice.
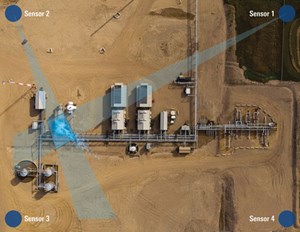
Permanently installed cameras provide valuable context about leak root causes. Open path laser networks, employing a central laser emitter and detector that reflects a laser beam off multiple perimeter mirrors, may be optimal for monitoring large areas containing
many sites.
With all of these technologies available, careful technology selection is essential. Higher performance—in terms of improved frequency, improved sensitivity, or other improvements—typically comes at a higher cost, and the optimal technology for one asset may perform quite differently for another asset. Organizations with deep knowledge about both oil and gas facilities and new detection technologies can design optimal programs for emissions detection. Over the past several years, Schlumberger has evaluated more than 100 measurement technologies in indoor and outdoor laboratory environments to assess performance and robustness.
FIXING METHANE EMISSIONS
Leaks can be fixed, but equipment that deliberately vents gas to the atmosphere must be modified or replaced. For the most part, these are fast, cost-effective changes for operators to adopt.
Vapor recovery unit (VRU). VRUs capture vented gas from storage tanks or recovery towers. The captured gas can then either be re-injected into the formation, added to the pipeline and sold, or used as on-site fuel. As permitted venting levels are expected to drop dramatically, many more VRUs will likely need to be installed to capture formerly vented gas.
Instrument air system (IAS). Gas pressure-driven pneumatic equipment vents methane to the atmosphere, often in off-grid sites. The IEA estimates that replacing or modifying pneumatic controllers and pumps would, alone, cut 15% of global oil and gas methane emissions. Instrument air systems substitute compressed air for pressurized natural gas, but require a compressor which, in turn, must be powered by solar electricity or gas where grid power is not available. Other replacement options include mechanical controllers or swapping high-bleed pneumatic devices for low-bleed equipment.
Leaky or venting valves. Tried-and-tested low-emissions (Low-E) valves can reduce fugitive emissions by up to 96% when compared to non Low-E valve products. Over the past several years, Schlumberger’s Cameron business has developed new sealing technologies to meet the most demanding applications and certified its existing valve designs to the API 624, API 641 and ISO 15848 standards, which are generally considered the gold standards for Low-E certification for valves. Today, more than 95% of the company’s valves are Low-E certified, Fig. 4.
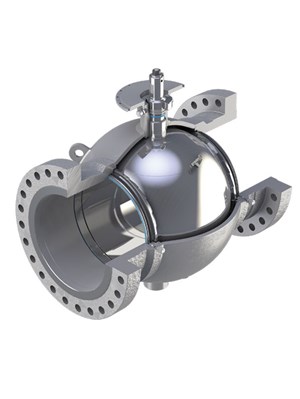
Flaring as remediation. Where no other alternative to venting exists, there’s flaring. Because CO2 has less than 4% of methane’s greenhouse warming effect, it’s far better to flare methane than to release it unburnt.
FILLING THE GAPS
Many of the existing shortcomings in methane reduction technology are now being addressed, but some critical gaps remain. For example, monitoring emissions offshore remains a major challenge, as most sensor technologies are ineffective there.
Current remediation equipment is often intended for larger facilities and applications. For example, VRUs and IASs are typically uneconomical for smaller facilities which, nevertheless, contribute substantially to emissions.
Flare monitoring is the biggest gap of all. Effective, accurate flare monitoring and optimization systems have yet to reach the market. Schlumberger is currently developing an optical measuring tool to quantify combustion efficiency and minimize unburnt gas.
For flare abatement in remote locations, converting the gas to a marketable product is one way to reduce emissions and generate revenue. The industry often refers to this process as “gas-to-X.” Using gas for local power generation or converting it to LNG and storing it for periodic tanker transport are two conventional solutions. New gas monetization options are appearing here,
too, such as conversion to agricultural feedstocks.
Schlumberger is field-testing a new simulator technology that takes into account flare gas composition, volume and physical location to perform a comprehensive techno-economic evaluation. The simulator leverages the thermodynamic engine of Schlumberger’s Symmetry* process software platform to identify which gas monetization option will maximize net income for the operator.
THE ROLE OF DIGITAL
Digitally enabled devices and software applications are crucial to future methane reduction, from autonomous drones and sensor signal processing to the image recognition algorithms that will automate continuous OGI camera operation. Existing applications like the Symmetry platform (Fig. 5) used for gas processing equipment design can already help estimate methane emissions from a facility and quantify emissions from known methane-emitting equipment.
But leveraging digital devices and IoT creates challenges of its own. The data flowing from many thousands of devices requires centralized processing—standardization, data quality checks—and integration to make it reliable and actionable. Sensor data must be consistent and comparable, regardless of technology or vendor, or any baseline emissions estimates will be less meaningful or effective.
Creating a central platform makes that high-quality, trusted data accessible, able to flow into today’s systems and familiar business intelligence (BI) tools: KPIs, dashboarding and reporting. The benefits for management and operational planning, forecasting and day-to-day decision-making are clear.
Once in place, a central platform also supports transformational automation and analytics, whether it’s automated satellite leak monitoring, AI-driven optimization or predictive recommendations. This will maximize both the efficiency and methane reduction effectiveness of operations and maintenance activity.
Project Astra gives a foretaste. Schlumberger is working with the University of Texas, Chevron, ExxonMobil, Pioneer Natural Resources Company, Microsoft, GTI and the EDF to develop a smart monitoring system that analyzes survey data from a large sensor network. It will provide near-continuous emissions monitoring across oil and gas facilities in high-density regions, such as the Permian basin.
The system will reduce monitoring costs by minimizing sensor numbers, identifying sites with leaks, and feeding data to a central system. That can then be used to quickly notify field response crews, speed repairs and cut costs while increasing the amount of methane detected.
A mature digital platform like this can integrate disparate systems and provide access to open, standardized data. That supports a multi-vendor equipment strategy where multiple sensors can communicate with each other and their data can reliably be combined and analyzed.
THE HOLISTIC APPROACH
For many operators today, methane abatement is an ad hoc, tactical activity handled by their HSE function with limited resources. But the scale and urgency of the task now requires a board-level focus.
That means bringing HSE together with asset teams and other functions while forming strategic partnerships with suppliers. With a centralized business unit and systems that span all reduction activities, a program of continuous learning and improvement is possible, with synergies available across technologies and operations. In time, methane reduction will become business as usual. But not yet.
Solutions will be different for every operator. One may prioritize leaks and vents, while flaring will be the main focus for others. Some operators may want an end-to-end set of services, others may have more focused needs.
Emissions management is a fast-evolving specialty. Many operators are still learning to handle it effectively and efficiently. Numerous tools and technologies for methane reduction are already available and understood but, as demand rises, vendors are innovating. Many solutions involve technologies foreign to oil and gas and require specialist advice to evaluate and integrate.
However, that selection has to be made with their oilfield application in mind—which requires oil and gas expertise. Setting strategy, understanding regulation, evaluating both available and emerging technologies, choosing vendors, combining solutions and scaling them globally: it’s a complex challenge.
Schlumberger is currently working with operators to accelerate their methane reduction programs. For example, many operators are interested in understanding the pathway to certification by the Oil and Gas Methane Partnership (OGMP). Backed by the UN, the OGMP’s methane reporting framework is widely supported by the global energy industry. A recent Schlumberger study for an IOC identified and analyzed gaps in its methane emission reporting, resulting in a multi-year work plan and budgetary estimates that will allow it to reach OGMP 2.0 Gold Standard.
THE CORRECT BUSINESS CHOICE
Tackling methane emissions offers a huge opportunity for our industry to make a difference quickly. By doing it now and doing it right, it’s possible to have a meaningful and measurable impact on global warming reduction.
This is not altruism. Any industry players that ignore the rising pressure from all sides to reduce methane and all GHG emissions are risking their reputation, share price and continuing operation.
Legislation now before the U.S. Senate proposes federal methane fees intended to curb emissions. Advocacy group EDF is currently measuring operators’ methane emissions in the Permian basin and listing results on its website. It plans on launching its own satellite—MethaneSAT, which will have the capability to measure facilities globally without requiring access to the site.
In 2020, the French government blocked a $7 billion LNG deal, due to excessive methane emissions—generated in Texas, not France. Proposed EU legislation will require energy producers and potentially importers to report their international methane emissions, with “more stringent” measures planned from 2025 onwards.
This issue threatens the entire global industry and the world is watching. The solutions required are largely here now, but choosing and deploying them successfully demands a considered, holistic approach. To get this right, the industry needs to work collaboratively with experts, who can help them develop an emission reduction strategy and select the most appropriate combination of technologies to achieve their objectives.
REFERENCES
- Methane Tracker 2021, IEA, Paris, 2021. https://www.iea.org/reports/methane-tracker-2021
- Jackson, R. B., M. Saunois, P. Bousquet, J. G. Canadell, B. Poulter, A. R. Stavert, P. Bergamaschi, Y. Niwa, A. Segers, and A. Tsuruta, “Increasing anthropogenic methane emissions arise equally from agricultural and fossil fuel sources,” Environmental Research Letters, Vol. 15, Number 7, 2020. https://doi.org/10.1088/1748-9326/ab9ed2
- Beck, C., S. Rashidbeigi, O. Roelofsen and E. Speelman, “The future is now: How oil and gas companies can decarbonize,” McKinsey & Company, 2020. https://www.mckinsey.com/industries/oil-and-gas/our-insights/the-future-is-now-how-oil-and-gas-companies-can-decarbonize
- Brandt, A. R., G. A. Heath,and D. Cooley, “Methane Leaks from Natural Gas Systems Follow Extreme Distributions,. Environmental Science & Technology, 50(22), pp. 12512–12520, 2016. https://pubs.acs.org/doi/10.1021/acs.est.6b04303
- Rashid, K., Speck, A., Osedach, T.P., Perroni, D.V., Pomerantz, A.E., “Optimized inspection of upstream oil and gas methane emissions using airborne LiDAR surveillance,” Applied Energy, Vol. 275, 2020. https://doi.org/10.1016/j.apenergy.2020.115327


- Coiled tubing drilling’s role in the energy transition (March 2024)
- Advancing offshore decarbonization through electrification of FPSOs (March 2024)
- Digital transformation/Late-life optimization: Harnessing data-driven strategies for late-life optimization (March 2024)
- The reserves replacement dilemma: Can intelligent digital technologies fill the supply gap? (March 2024)
- Digital tool kit enhances real-time decision-making to improve drilling efficiency and performance (February 2024)
- Executive viewpoint: TRRC opinion: Special interest groups are killing jobs to save their own (February 2024)
- Applying ultra-deep LWD resistivity technology successfully in a SAGD operation (May 2019)
- Adoption of wireless intelligent completions advances (May 2019)
- Majors double down as takeaway crunch eases (April 2019)
- What’s new in well logging and formation evaluation (April 2019)
- Qualification of a 20,000-psi subsea BOP: A collaborative approach (February 2019)
- ConocoPhillips’ Greg Leveille sees rapid trajectory of technical advancement continuing (February 2019)