Adjustable smart-bit increases durability and ROP during drilling operations
Polycrystalline diamond compact (PDC) drill bits have seen consistent improvements in durability and efficiency to support enhanced operating parameters as well as BHA designs that include powerful motors and sophisticated rotary steerable systems. These performance gains are largely the result of improvements in the toughness and durability of the PDC cutters themselves, but design features and relentless iterative product development have also played a part.
While R&D resources are being applied to PDC bit development, the key performance indicators for drill bit applications are becoming somewhat restrained. It’s difficult to reduce the number of bits per section when most hole sections are already drilled with one bit. It is equally challenging to significantly increase ROP when hydraulic configurations cannot efficiently evacuate drill cuttings up the annulus. Additionally, wellbore quality and directional requirements sometimes override the desire to drill faster.
As a result, one innovation that can drive further performance gains is broadly categorized under the label of “smart bits.” At National Oilwell Varco, the ReedHycalog business unit has moved to the forefront of the smart bit market, developing technologies that measure various aspects of the drilling environment, communicate those measurements, and modify themselves downhole based on that information.
KNOWLEDGE IS POWER
High-frequency measurement of downhole parameters and vibrations became part of the ReedHycalog portfolio in the late 1990s. Since then, the company has continued to develop and deploy new measurement technologies for internal research, product development, and drilling optimization projects. Near-bit and at-bit measurements are a significant advancement that provided NOV product engineers with crucial information as they worked to improve the drilling efficiency of PDC bits. Engineers also discovered that near-bit and/or at-bit measurements could be combined with measurements farther from the bit to improve BHA models, overall directional control, and the stability of the drilling system.
Drilling parameter and vibration measurement tools are now incredibly accurate and gather data at an impressive frequency. Once processed, the data can provide significant insights into downhole dynamics and efficiency as well as less obvious topics such as wellbore quality and formation characteristics. By taking these measurements at the bit rather than several feet above within the BHA, it provides an immediate look at many aspects of the drilling process as well as information on the formations bring drilled.
One intriguing application for these downhole measurements is the potential to use the data in neural network or big-data analyses. If we can capture downhole data across the entire depth of many wells within a field, we can draw new conclusions about drill bit selection and BHA design, parameter optimization, and geological trends. Many of these statistical analyses can be automated—the limiting factor is the availability of a high volume of quality data.
The relative high costs related to many types of measurement tools have limited their deployment, and, as a result, typically less than 10% of wells in a given application will include tools that capture high-frequency data. ReedHycalog is working to improve these statistics.
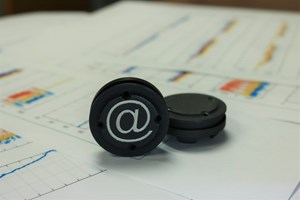
To improve the accessibility of near-bit, downhole data acquisition, the service provider is currently deploying a small, low-cost data recorder that records and stores data on all ReedHycalog PDC bits in specific applications. The @bit recording device is a 1.6-in. diameter plug that fits securely in the shank of any bit using a 4½-in. API pin or larger, Fig. 1. The recorder has a 15,000-psi maximum pressure and a 257°F maximum operating temperature. Even with its tiny size, the @bit device is capable of 100 Hz sampling rate and 200 hr of operation in the downhole environment while recording three-axis vibration, downhole temperature, and RPM.
Throughout the development of this tool, the emphasis has been on ease of use. The @bit device does not affect the BHA design, and the carrier takes minutes to install or complete its data download. By making the @bit device affordable, both in terms of hardware and manpower for implementation, it can be broadly deployed across a target field.
Due to its extremely small size, the device cannot store large amounts of data. However, it automatically processes data while downhole and stores that information for when it is needed to support decisions about the dynamic performance of the bit.
The @bit data are collected post run in an almost completely automated system, further reducing the expense of analysis. A simple, one-page report is automatically generated, providing vibration statistics for the run that are broken down by day. The data are indexed and uploaded to a database where drilling experts can work with operators to analyze performance trends via a map interface.
Applying smart adaptation to reduce bit trips. As previously mentioned, many hole size sections around the world are now drilled with a single bit, which is a result of advances in drill bit durability as well as improvements in other drilling systems such as motors, rotary steerable tools, and MWD components. Considering the costs of tripping in and out of hole, which are particularly high in offshore applications, this is a significant development from the viewpoint of operator costs.
The downside to this reduction in bit changes during the drilling process is that once the drill bit has been selected and run downhole, that same bit will often be used to drill many different formation types under different pressure and hydraulic regimes. The same bit can potentially be tasked with varied directional objectives, as well—all while drilling at a high ROP.
In most cases, the driller typically has limited control over the drilling performance optimization that has been committed to the well plan, with input mainly based on operating parameters. This emphasizes the importance of good parameter planning, bit selection, and BHA design. However, compromises must be made in most plans due to the changing downhole conditions throughout the run.
To address this challenge, ReedHycalog has developed a new technology that allows the bit to adapt and change while downhole, thereby eliminating a trip to surface. The new technology offers the potential for bits to adapt to changing dynamic environments, formation characteristics, directional requirements, and more. In this way, the bit can drill at the highest possible efficiency for the entirety of its downhole lifecycle—improving ROP, wellbore quality, and directional profile while reducing the likelihood of catastrophic failure for the bit or BHA components.
Current testing of these “smart-adapting” bit concepts is allowing the driller to deploy additional cutting structure or depth-of-cut limitation elements during the drilling process. In the first prototype of this technology, the adaptation is triggered via changes in hydraulic parameters, but future versions will utilize other deployment methods. The technology can be deployed in several valuable ways.
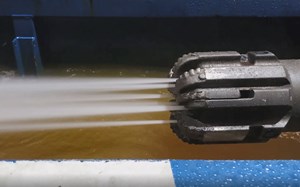
In one such example, a driller selects a bit that drills very aggressively through the first half of an application, where the formations are relatively soft. To accomplish this, a relatively light-set bit with six blades would be used. As the drilling operation encounters extremely abrasive sands, the six-blade bit that worked so well in the top of the hole will not survive this section as noted in offset wells, requiring a costly trip for a new, application-specific bit. With ReedHycalog’s smart-adapting bit technology, a driller can deploy additional blades with fresh cutters, providing enhanced durability so the BHA can finish the section without pulling out-of-hole to replace the dull bit, Fig. 2.
The smart-adapting drill bit can also benefit directional applications, in which the curve and horizontal sections are drilled with a single hole size. For the curve, depth-of-cut control is required on the bit in combination with a bent-housing motor to ensure a smooth torque response. To accomplish this, the smart-adapting bit deploys depth-of-cut control elements that reduce torsional fluctuations and tool face control issues. However, after completing the curve, offsets show the lateral can be drilled at an ROP three or four times faster than what is achieved in the curve. In this case, the smart-adapting bit can retract the depth-of-cut control elements to allow greater penetration of the cutting structure, allowing the bit to drill the horizontal as quickly as possible, Fig. 3.
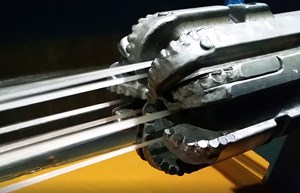
In addition to these operational benefits, other scenarios include the ability to significantly change the cutting structure, gauge configuration, and/or hydraulic design while downhole to further optimize performance.
New synergies going forward. As technology and material science advance, new at-bit measurement products will be developed by the industry, leading to information provided in real time for drilling optimization, as well as in memory for post-well analysis. Drill bit suppliers and operating companies must work together to identify what information from the bottom of the well provides the greatest value and how quickly those data are needed to maximize value.
Smart-adaptive bit control can be exerted from the surface via various downlink methods that are already in use around the industry. Ultimately, these methods may be too time consuming and not provide the reactive control needed.
Smart-adaptive bit development should be working towards systems that require no direct interaction with surface personnel. As these smart bits acquire measurements, those data should be combined with measurements from other tools in the BHA, as needed. When the required information is in place, the bit (and other portions of the BHA) should then react and adapt to the changing conditions without interference from the surface. These closed-loop capabilities have the potential to dramatically improve drilling efficiency and improve processes such as geo-steering and at-balance drilling as smart bit designs progress in the coming years.
- Coiled tubing drilling’s role in the energy transition (March 2024)
- Digital transformation/Late-life optimization: Harnessing data-driven strategies for late-life optimization (March 2024)
- The reserves replacement dilemma: Can intelligent digital technologies fill the supply gap? (March 2024)
- Digital tool kit enhances real-time decision-making to improve drilling efficiency and performance (February 2024)
- E&P outside the U.S. maintains a disciplined pace (February 2024)
- U.S. operators reduce activity as crude prices plunge (February 2024)
- Applying ultra-deep LWD resistivity technology successfully in a SAGD operation (May 2019)
- Adoption of wireless intelligent completions advances (May 2019)
- Majors double down as takeaway crunch eases (April 2019)
- What’s new in well logging and formation evaluation (April 2019)
- Qualification of a 20,000-psi subsea BOP: A collaborative approach (February 2019)
- ConocoPhillips’ Greg Leveille sees rapid trajectory of technical advancement continuing (February 2019)