Drilling Advances
While the definition of what constitutes an offshore or onshore rig as fully prepared for managed pressure drilling (MPD) varies widely, it is generally acknowledged that blanket adoption of MPD will remain elusive until the technology is universally perceived as an efficiency driver, rather than strictly a mechanism for drilling cantankerous wells.
“When we drill a well with MPD trouble-free, usually the first response is ‘we didn’t need it’,” Dennis Moore, senior technical consultant at Marathon Oil Co., said while moderating a panel discussion during the IADC Drilling Engineering Committee’s (DEC) quarterly technology forum in Houston on Sept. 19. While the six-member panel—split between operators, contractors and service providers—offered different perspectives on the meaning of MPD-ready, it was agreed that a business model that positions the multi-variant technique as a cost-effective, performance drilling tool is long overdue.
“Even though it’s proven that MPD improves well efficiency and reduces NPT (non-productive time) and risk management, we often find, especially in deepwater, that MPD comes with a high price and long lead times that make it hard for many operators to actually justify it,” says Wael Essam, BP’s managed pressure team leader.
“Having a rig equipped with all the latest and greatest equipment doesn’t mean it necessarily is ready for MPD today. You have to look at all the things that define that capability. It’s just not about the equipment, but having competent people to run the equipment. It must be integrated into the rig management system and the safety management system. And, looking at the big picture, you have to decide who’s responsible for what, and who accepts the liability.”
Shell is orchestrating installation of an MPD package on Transocean’s Deepwater Thalassa drillship for a deepwater Gulf of Mexico program, and agrees that proving value must be at the forefront. “In general, we want to use MPD to navigate narrow margins on a couple of our wells, but overall, we want to reduce NPT and increase drilling efficiency,” said Roger van Noort, well engineering team lead, North American–Nova Scotia and MPD implementation. “Ultimately, it has to be supported with a value generator. If you increase ROP with a bit, for instance, you look at the offset data, and calculating the business value is easy. If you say that the NPT went down for all my rigs, that’s probably all you need to justify MPD.”
Rent or own? For drilling contractors, the biggest question is whether to rent or own the MPD packages on their rigs. Transocean, which has employed various MPD techniques on more than 80 offshore wells, leans toward the former. “I personally view MPD like well test equipment,” says Technology Manager John Kozicz. “The rig should be prepped with piping in the right spots, all the services in place, and all the hazardous zones identified. So, it doesn’t matter whose kit you use. From a drilling contractor’s perspective, that’s the easiest way to view MPD equipment.”
With five MPD-enabled deepwater rigs, Seadrill prefers taking ownership, but doing so poses daunting personnel challenges. “After five iterations of this, it’s become clear that the human factors are probably the greatest challenge we face as an owner-operator,” says Jay Lancaster, MPD/well control technical superintendent. “It involves the integration of the procedures and maintenance aspects, the integration of training, the integration into the company safety management systems, and the acceptance of new techniques by the crew.”
No size fits all. The onus of complying with myriad end-user specifications falls squarely on MPD equipment designers. Ideally, the goal for service providers is to design, and build, equipment and associated control software that meet minimum specifications, which first requires that the industry agrees on a definition of MPD preparedness.
“When operators put out tenders for MPD-ready rigs, you might have 100 rigs checking the boxes to say they’re MPD-ready, because the industry hasn’t defined it to the point that we really understand what that means,” says Neal Richard, Weatherford global line manager, well integrity. “When I say I’m prepared for MPD, does that mean I’m prepared for constant bottomhole pressure, or that I’m prepared for riser gas handling? “
Richard concedes that global standardization and integration of MPD packages on rigs that meet minimum specifications is at the mercy of divergent client requirements. “So often, we’re called by an operator or drilling contractor, who say they want to install an MPD system on a rig, but they come with their own specific requirements, so it’s difficult to provide standardized packages, when the specifications of clients are constantly changing.”
Weatherford, for instance, has completed more than 50 deepwater MPD installations, and no two have been alike. “What we’ve learned is every single rig-up is different. We’ve never been able to mimic one rig-up to the next,” Richard said.
Schlumberger focuses on developing basic technology blocks, like rotating control devices (RCD) for various applications, with a charter to lower the barrier of adoption and make MPD readily available, says Blaine Dow, drilling engineering marketing and technology manager. With operators’ objectives differing, well-to-well, and even between hole sections, standardizing an entire MPD kit is a difficult proposition, he says.
“By focusing on specific technology blocks, we enable the contractor, operator and service provider to collaborate on an installation and approach it as a project. As each one has to be customized, it’s not so much product development, as project management, and it needs to be looked upon that way,” he said.
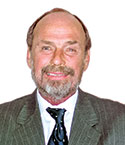
- Applying ultra-deep LWD resistivity technology successfully in a SAGD operation (May 2019)
- Adoption of wireless intelligent completions advances (May 2019)
- Majors double down as takeaway crunch eases (April 2019)
- What’s new in well logging and formation evaluation (April 2019)
- Qualification of a 20,000-psi subsea BOP: A collaborative approach (February 2019)
- ConocoPhillips’ Greg Leveille sees rapid trajectory of technical advancement continuing (February 2019)