STEVE JACOBS, Decision Strategies
As the oil and gas shale revolution continues to expand in North America, a significant number of technology-oriented events are taking place that merit investigation. Unconventional plays seem to evolve in complexity, with new technology needed to exploit the uniqueness of each unconventional field. To identify and address the important trends occurring with shale technology, World Oil and Decision Strategies jointly conducted a market survey among North American operators and technology providers. (The survey was developed by the ShaleTech work team, which has created a special World Oil supplement, and the ShaleTech conference, to be held in Houston, Aug. 28-30, 2013.)
Some of the important issues covered include drilling, geoscience, and hydraulic fracturing and water management challenges. All major shale plays are represented in the survey sample, including the Eagle Ford, Bakken, Marcellus, Barnett, and Haynesville shales, etc. The opinions of more than 135 participants in shale plays throughout North America are summarized in this article.
NEXT BIG SHALE PLAYS
After identifying the various oil and gas shale plays where the survey respondents were active, each was asked: “What will be the next big shale play” in various areas of the world. The results were interesting.
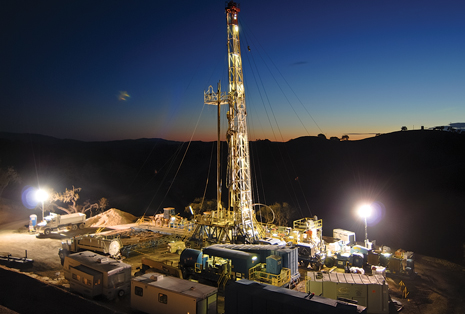 |
Fig. 1. Although politics and regulatory hurdles could get in the way, a majority of survey respondents nonetheless believe that California’s Monterey shale is the next emerging play. Photo courtesy of Underground Energy Inc. |
|
In the United States, the Monterey shale (Fig. 1) in California was, by far, the most frequently mentioned emerging shale play. Running from Modesto, south to near Los Angeles, this play has considerable potential, but it also faces technical challenges, and political issues with state and local municipalities. In Canada, the Duvernay formation was the most frequently mentioned, emerging shale play. There were also a few mentions for development of the Canadian side of the Bakken. By far, the most frequently mentioned unconventional play within the international marketplace is Vaca Muerta field in Argentina.
ADDRESSING EMISSIONS ISSUES
Concurrent with any discussion of shale technology is the need to address emissions issues related to high-horsepower applications. Emissions have become an extremely important topic, as considerable attention is being given by U.S. government entities and the general population to drilling, stimulation and production activities in the last few years. In an important survey question, operators were asked: “How is your company reducing emissions from rig and fracing operations?” The chart in Fig. 2 illustrates a somewhat surprising outcome, in that the move to natural gas as a fuel source for high-horsepower engines was mentioned by almost half the participants in the survey.
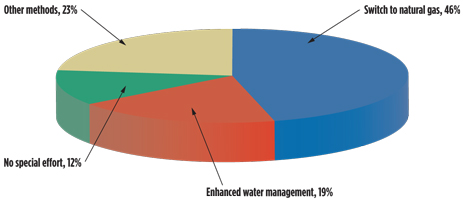 |
Fig. 2. Methods mentioned by respondents for reducing rig and frac emissions. |
|
One operator provided an interesting list of examples regarding the use of natural gas for drilling rigs, frac spreads and service vehicles—“Using new technologies, such as converting drilling, service and frac fleets over to natural gas from feedstock of existing wells. Also, electric-powered frac equipment with the power supply from a portable natural gas-fired turbine that uses feedstock from existing natural gas wells, brought in by use of temporary, above-ground pipelines that can be removed after project completion.” Clearly, there are some creative practices being developed for reducing emissions from drilling rig and frac spreads.
In addition to the increased use of natural gas, some operators also mentioned utilization of bi-fuels as a way to reduce emissions. In fact, in early experimentation with natural gas–powered engines, efforts are being made to use both diesel and natural gas intermittently, to optimize overall rig performance. Engine manufacturers are also providing retrofit “kits” that allow diesel units to run on natural gas.
A few oil service companies also addressed this question, outlining the reduction of high-horsepower needs, lowering truck traffic to and from the well site, and using more “green completions.”
Water management issues were a common topic, when respondents were asked to identify trends in shale plays and related technology. One operator listed several water management-related steps being taken to reduce emissions—“Optimize friction reducers, water volumes, water temperature specs. Use of bi-fuel diesel/natural gas engines, water source piping versus trucking, a centralized frac water storage site, and the potential use of water-based drilling fluids.”
A range of other activities is being pursued to address emissions issues. These include smaller rig and equipment footprints; pad drilling to reduce rig moves; reduced flaring; and utilization of more energy-efficient rigs and transportation.
MOST SIGNIFICANT TECHNOLOGY
Undoubtedly, there is additional technology required to more efficiently exploit oil and gas shale plays in North America. To identify these needs, the respondents were asked, “What is the single technology you believe will make the most significant difference in optimizing oil and gas shale production in North America?” Mentioned with most frequency were hydraulic fracturing, water management, and drilling optimization, Fig. 3.
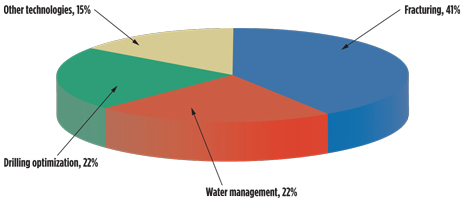 |
Fig. 3. Fracturing was the single method mentioned most often by survey respondents for optimizing shale play production. |
|
Regarding hydraulic fracturing, particular focus was given to the analysis of fracs, to optimize their effectiveness. As stated by one operator, “Understanding why only 25 to 30% of the hydraulic fractures in any given horizontal well contribute to production. If we can do a better job of deciding which rock to stimulate, then we can reduce the completion and fracing charges significantly.”
Oil service company personnel participating in the survey focused primarily on emerging frac technologies and improvements in water management. Two comments from service providers are of interest. The first respondent said, “Optimizing frac stages and volume, based on acres drained. We have to reduce water and proppant pumped per well. The cost reduction will help independents produce more oil and gas per dollar spent. This will reduce energy wastage and polluting emissions.”
The second respondent added, “An artificial lift method to de-water horizontal gas wells. There may be well over 1,500 wells shut in in the Barnett area, alone, due to loading of water in the lateral, thus stopping production.”
In addition to water management (which will be discussed later in this article), considerable significance was also attached by operators to several types of drilling optimization technology. Understanding and optimization are the keys to drilling efficiency within the North American shale play sector. One operator said that “drilling enhancements to drill faster and more accurately equals driving down costs. This will allow companies to access formations with horizontal technologies, which were uneconomic a few years ago.”
Another operator commented that his needs included “reliable and affordable, compact MWD/LWD tools to really see what the formation looks like before we set up frac stages. Many frac stages are still a blind guess without really knowing how to optimize from a reservoir perspective. Big initial productions are great for the press releases, but if you don’t know the oil-in-place, how do you really evaluate success?”
Other important technologies mentioned infrequently include enhanced completion equipment, permanent downhole monitoring, chemicals, multi–laterals, etc. Additionally, a few operators discussed the need for enhanced proppants.
DRILLING TECHNOLOGY CHALLENGES
Oil company personnel engaged in drilling operations were next asked, “What are your drilling technology challenges in oil and gas shale plays?” Generally the oil company personnel were relatively satisfied with current drilling technology. However, technologies cited as needing improvements include rotary steering, mud motor reliability, well control, environmental issues, etc. One operator summarized these drilling issues well—“The biggest challenges that I’ve encountered are having to pull out of the hole, due to mud motor failures, bit failures, or failure to achieve build rates. Most of these problems can be attributed to not knowing the optimal BHA to use in this field and needing more data, or trial-and-error.”
When asked what “new or pending technologies will make the drilling of oil and gas shale wells more productive” the most frequent response was “enhanced rotary steerable systems,” Fig. 4. According to one operator, “Rotary steerables allow continuous rotation to improve hole cleaning. Rotary steerables also create a less aggressive hole geometry, which allows casing to be run in the hole easier.” As might be expected, when operators were asked what would accelerate the rate of acceptance of these new drilling technologies, the most frequent response was a lower cost for the product or service being introduced. An interesting comment from an oil service company representative was the need for developing “a subsurface equivalent to GPS.”
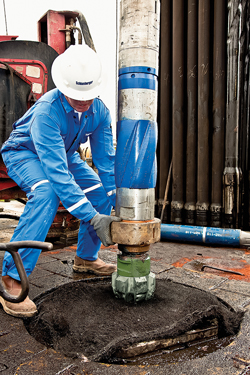 |
Fig. 4. Enhancement of rotary steerable systems is the advancement that a majority of survey respondents feel will make the drilling of shale wells more productive. Photo courtesy of Schlumberger. |
|
The respondents were next asked: “What non-technical issues, such as regulations, infrastructure or workforce availability, need to be addressed within the shale play drilling sector?” Concerns about workforce availability were expressed, regarding “both quality and quantity of a highly skilled workforce.” This operator comment was one of the more interesting ones made—“Logistics and people. Shale plays are a numbers game. Frequency of wells will mean larger gains. To obtain such a high drilling rig count, one has to have an infrastructure that supports all services and tool availability. North America has the existing infrastructure, but most of the international shale plays might not. People availability, worldwide, could be another major roadblock.”
A few oil service company representatives stated the need for a more skilled workforce within their local areas (such as West Texas).
GEOSCIENCE TECHNOLOGY CHALLENGES
Geoscientists within oil companies also participated in the World Oil survey. They had some interesting comments, when asked what their technology challenges are for oil and gas shale plays in North America.
One respondent said that his challenges include “natural fracture characterization and ductility prediction from 3D seismic. How do you accurately describe in situ reservoir permeability?” Another participant replied, “Interpreting variations in lithologic characteristics along Hz wellbores and utilizing seismic data to interpret lithology and characteristics of target shales.” A third respondent stated, “The hydro-frac reservoir is way more complex than can be modeled—you still have to make a large amount of assumptions.”
One of the more interesting oil service company comments addressed a broader issue—“1) A process to determine the minimum data needed to make informed decisions. 2) A platform to store and leverage data to make necessary changes in field development planning. 3) A tool to back-test how your changes (e.g. strategy) would turn out, based on historical data or models similar to the financial industry.”
The geoscientists were next asked: “What new or pending technologies will help improve reservoir characterization?” While few answers were given with significant frequency, the integration of rock properties, use of micro-seismic, better core analysis technology, and enhanced frac and stimulation models were identified. When asked what would accelerate the rate of acceptance of these new geoscience technologies, the primary responses were “providing proof” and “acceptable data.”
The few geoscientists identifying new technology for reservoir characterization focused on seismic imaging and processing. According to one service company representative, “There is a new, integrated technological solution for geoscientists to do quantitative interpretation in oil and gas shales in 3D (away from well control, and extended to overburden and underburden) to predict reservoir quality and performance indicators in a single platform….It allows any geoscientist to perform simple-but-robust analysis and modeling of oil and gas shale properties using integrated modules.”
Asked what would accelerate the rate of acceptance of new geoscience technology, lower cost, and having operators make a fair investigation into the merits of these technologies, were mentioned by oil service company representatives.
COMPLETION TECHNOLOGY CHALLENGES
Hydraulic fracturing and extended reach drilling are commonly recognized as the technology enablers for North American unconventional fields. If fact, without these two technologies, there would be no need to write this article. Operators in completion positions were asked, “What are your technology challenges in completions, including hydraulic fracturing?” The most common responses were water optimization and utilization, along with new technologies.
One respondent said, “If the operators could work together, we could even-flow the work and give the frac contractors time to maintain their equipment and safely train new hires. If we all took more time to plan, we would get more done. It’s a manic rush to get everything done right now, and safety and efficiency are suffering.” A second participant said his challenges included “limiting the use of fresh water, and introducing new technologies and infrastructure to reduce/replace diesel-powered equipment. Treating produced fluids in remote areas for re-use in other field applications in field operations/treatments.”
When service company representatives were asked to identify challenges in completions, including hydraulic fracturing, two interesting comments were made. One firm simply said, “Our major challenge is market acceptance.” (Several oil company personnel voiced similar concerns with public acceptance.) A second company complained that “the main challenge in fracturing is a tendency to overtreat, i.e., 1) Larger volumes; 2) larger amounts of proppant; 3) higher horsepower usage; 4) longer completion times; 5) greater risk; 6) 24-hr completions are a big mistake; 7) excessive cost of the completions; 8) less dependency on good geology and more on statistics.”
It was also important to discuss emerging shale play technologies. When asked, “What new or pending technologies will help improve fracing for shale plays,” several products and services were mentioned. These included the use of fiber optic monitoring, improved perforating charges, better completion tools, non-water-based fracturing fluids, and enhanced frac chemicals. These topics have been the subject of a number of market research assessments recently, which indicates that technology providers are planning on addressing these unresolved needs in the near-future.
Significant advancements in fiber optic technology have taken place in the last few years, resulting in more reliable and actionable downhole information. Regarding fiber-optic monitoring, the following operator comment was made—“At present, use of fiber-optic monitoring (e.g. distributed temperature sensors) is enabling real-time monitoring of proppant placement, and thereby, enabling a decision-making process based on actual sand mass placement. But deploying fiber optic in every single operation is expensive—hopefully, the technology, will be available at less cost in the near future.”
As to what would “accelerate the rate of acceptance of new hydraulic fracturing technologies,” mentioned most frequently were lower costs, positive test results and professional papers, and better service availability and infrastructure. Concerns were also stated about the need to educate the public. These views were well expressed by one operator—“The cost of new technologies is always the biggest stumbling block, so in my view, widespread acceptance by the industry as a whole, and investment in this, should be greater. Education of non-industry people is also a key factor.”
REDUCING HYDRAULIC FRACTURING COSTS
Considerable attention has been paid by operators to developing ways in which to reduce stimulation costs. Some oil companies have created their own stimulation services and negotiated long-term contracts with pumping service suppliers, while others are attempting to reduce water and chemical usage. Services also exist for fracing without the use of water. In an effort to identify the range of cost-saving activities, each operator was asked, “What is your company doing to reduce frac costs?”
Two operator comments are representative of those made by the respondent group, as a whole. One participant said that his company is “optimizing frac stage size and number of stages. Sourcing our own chemicals, to eliminate the surcharges that frac companies (charge) us with, when they use third-party chemicals.” Another respondent said his firm’s cost-cutting methods include “recycling, re-use of flow-back and produced water (Fig. 5), natural gas-fired equipment, and use of solar power, where possible, for low-power equipment on production operations.”
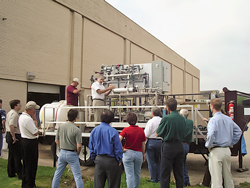 |
Fig. 5. How to handle produced water is a growing challenge in shale operations. During the mid-2000s, Texas A&M’s Global Petroleum Research Institute developed a portable produced water treatment system that can be moved into oil fields to convert produced water to potable water. The system was tested successfully on traditional wells, and researchers are now looking to adapt the technology to shale resources. Photo courtesy of National Energy Technology Laboratory. |
|
A few oil service company representatives addressed the cost issues raised by the operators. One service provider listed several cost-reduction steps that include “fracturing design to be done in-house by operating companies. Reduce fracturing stages—fewer pads, flushes, pre-pads, etc. Smaller number of wireline trips, fewer frac plugs by using differential frac technique, fewer plugs to drill out. I could conduct a whole-day seminar on this.”
When asked what “non-technical issues, such as regulations, infrastructure or workforce availability need to be addressed within the completion/fracturing sector,” several topics were mentioned. These items included: 1) dealing with public issues on hydraulic fracturing; 2) evaluating and complying with emerging regulations; and 3) addressing workforce requirements, where the availability of skilled personnel is inadequate.
As to issues with public perceptions of the petroleum industry, the following comment is worth evaluation—“Regulations and public perception are huge. The oil and gas industry has never been very effective in getting out the message about what we do. We always seem to be perceived in a negative light by the public, and I am not sure why that is the case. We need an improved image. I see that as the number-one non-technical issue that needs to be addressed.”
In addition, two oil service company representatives made interesting comments on workforce issues and pipeline regulations. The first person got right to the point, saying “There is a lack of qualified individuals, and operators/service providers look for experienced individuals. What they should be looking for are sharp, communicative individuals, who can pick up a new technology faster rather than look for laid-back individuals with just so much technical experience.” The second representative added, “Gas and oil pipeline regulations to move product are a huge regulatory issue. Public perception of dangers is not realistic, not based on science; just emotion and misinformation from certain environmental groups.” (Note: This does not change the fact that it is the petroleum industry’s responsibility to educate and indoctrinate public perception.)
Several oil service companies are worried about the cost and effort to comply with emerging regulations. Another respondent stated, “The U.S. regulators need to set up a service provider member support team, to make reasonable decisions.”
WATER MANAGEMENT CHALLENGES
Operators were also asked to identify their “technology challenges in water management for oil and gas shale plays.” This is a topic that has received considerable attention, both within and outside the petroleum industry, and is the subject of significant R&D efforts. There are also water resource issues in some areas of North America, where a lack of water exists for adequately fracturing all the wells drilled. Among the more salient water management comments made during the course of the survey, one operator said, “Cut down on the water usage in fracturing. Utilize local sources if possible. Consider gas fracturing with foam.” Adding to this, a service company respondent said, “We need to clean up the marketplace and publish case studies that frankly describe commercial successes and failures. We need to design post-frac flow-back procedures that are optimized for water reuse. Too often, the completion prognosis reads, ‘Turn the well over to flow testers for flow-back.’ If an operator asks me to recycle or dispose of tanks of vegetable soup, I'm going to spend 90% of my time de-bugging their completion procedure, and 10% of my time thinking about treatment technology.”
As to what new or pending technologies will make water management more cost-effective and environmentally safe, respondents infrequently mentioned the need for frac chemicals (including biosorbants, and guar polymer measurements in flow-back water), and membrane separation technology to clean up and help recycle water, along with water storage and transport systems. As to what would accelerate the rate of acceptance of these technologies, operators mentioned more environmentally friendly chemicals; efficient cost control; and improved produced water access at a reasonable cost.
Oil company personnel were also asked to discuss the non-technical issues, such as “regulations, infrastructure or workforce availability,” needed to address water management issues. Few comments were provided that have not already been addressed in this article. However, one interesting statement is worth evaluation—“Regulations will never go away. And we will see more regulations from different aspects to impose on fracturing operations. On top of that, the enforcement will be intensified. The infrastructure will improve, when the cost benefits are justifiable.”
In summary, the combination of hydraulic fracturing and extended reach drilling technology has revolutionized the upstream sector of the petroleum industry. However, as new shale plays emerge around the world, a need exists for technology advancements to unlock the uniqueness of these unconventional producing formations. The irony is that through increased usage of natural gas in high-horsepower applications, the industry is not only helping to lower emissions, but it is simultaneously developing new markets in North America, and elsewhere, for this plentiful fuel. 
The author
STEVE JACOBS is chief marketing officer for Decision Strategies, a petroleum management consulting firm specializing in strategy and market intelligence for operators, technology providers and investors. He is recognized as an expert in the evaluation of emerging technologies, and accelerating their rate of acceptance. |
|