JERRY GREENBERG, Contributing Editor
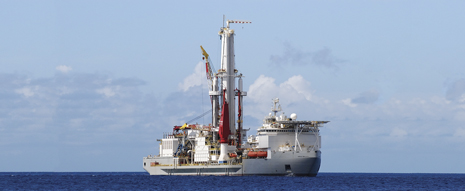 |
The Bully I drillship epitomizes the latest advances in offshore rig designs. |
|
Innovation in any industry should result in being able to do something more efficiently, less costly, with increased performance, or, ideally, all three. In the offshore industry, as operators wade into ever-increasing water depths accompanied by ever-increasing costs, drilling contractors, rig designers and equipment manufacturers assist in that effort by developing bigger, or sometimes smaller, but efficient equipment for deep and ultra-deepwater regions. Most of the innovation of making rigs and equipment better is aimed at the floating rig market, although one company has designed a jackup that is rated to drill in nearly 600 ft of water in North Sea conditions. Another company with deepwater drillship designs has a concept for a rotating cantilever for jackup rigs.
STATOIL DEVELOPS FLEET TO INCREASE OUTPUT
Statoil said that discoveries on the Norwegian Continental Shelf (NCS) are becoming smaller, thus it is important to increase drilling activity in mature fields, as well as exploit new discoveries to attain the NCS’ full potential. As a result, the operator noted five different types of rigs and vessels that would be necessary to maintain or increase production efficiently and economically, some of which already are in use, while others are under construction or for which tenders will be let this year. The company believes that a larger selection of rigs and vessels that are fit for purpose improves HSE, efficiency and cost. As a result, Statoil developed a list of five types (or categories) of vessels and rigs that it intends to use in its efforts to maintain or increase NCS production.
Among the rig types are semisubmersibles and jackups, including the CatD (Category D) rig (Fig. 1), a custom-built rig adapted to medium water depths on the Norwegian shelf. It can be used for drilling, completions and workovers, and can also be used for light well intervention and sidetrack drilling, wireline operations, coiled tubing, and plugging wells. Statoil tendered for a rig that would fulfill these operations and wound up contracting two new semisubmersibles from Songa Offshore in 2011, and contracted for two more semisubmersibles earlier this year. Statoil already had been contracting three rigs from the company.
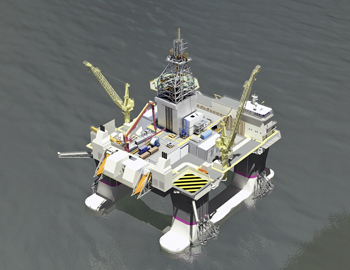 |
Fig. 1. The Songa Offshore rigs, Statoil’s CatD rigs, are based on the GVA 4000 design, rated to drill in up to 5,000 ft of water. The Songa rigs will be equipped for 1,640 ft (500 m) of water. The rigs, Songa Equinox, Endurance, Enabler and Encourage, are set for delivery in 2014 and 2015. |
|
Statoil originally tendered for semisubmersibles that could drill in up to about 5,000 ft of water. The Songa rigs are based on the GVA 4000 design that is rated to drill in up to 5,000 ft of water. However, they reportedly will be equipped to drill in up to about 1,640 ft (500 m) of water initially. The rigs, Songa Equinox, Endurance, Enabler and Encourage, are set for delivery in 2014 and 2015. The rigs will be capable of year-round drilling on the NCS and in the North, Norwegian and Barents Seas. There will be an operational goal that they perform 20% more efficiently than conventional rigs.
The common design of the four rigs allows for the interchangeability of parts, equipment, crew and other resources, leading to an overall savings in average operating costs. The rigs are designed, and will be built, to be compatible with all of Statoil’s subsea systems. The rigs’ BOPs, riser tension and compensation systems are designed for existing wellhead templates, with a focus on wellhead fatigue. Each rig is contracted by Statoil for eight years.
Daewoo Shipbuilding & Marine Engineering Co. (DSME) in South Korea will build the rigs at a fixed price of $570 million, each, inclusive of optional Statoil upgrades that include Barents Sea winterization and other enhancements. To reduce risk and secure yard capacity when Statoil awarded the drilling contracts, the operator reserved slots at Samsung Heavy Industries, Keppel FELS and Jurong Shipyard, in addition to Daewoo.
In addition to the Songa Offshore semisubmersibles, Statoil also sought jackup rigs for its effort to improve production. It recently contracted Maersk Drilling to provide a new GustoMSC CJ70 class jackup for delivery in 2015. This order was made as part of Statoil’s Category J (CatJ). The rig will be built at Keppel FELS. As with the Songa rigs, Statoil reserved shipyard slots at Daewoo, Samsung, Hyundai Heavy Industries and Jurong. Maersk operates a fleet of several GustoMSC jackups, including its largest, the CJ70 design. At one time it was thought that Maersk would offer an even larger rig. GustoMSC’s CJ80-175 jackup is rated for drilling in up to 575 ft (175 m) of water.
Maersk’s CJ70 rigs are rated to operate in up to 500 ft of water (450 ft in North Sea conditions) and drill to 35,000 ft. A unique feature is the X-Y cantilever system that combines the cantilever and drill floor structures into one fixed package that can move longitudinally and transversely, relative to the hull. This means there is no need to disconnect the BOP, cables, hoses, etc., when moving the drilling package, since there are no flexible lines between the cantilever and drill floor. The design results in simplified BOP handling and a minimum of deck obstruction. Additionally, the cantilever’s elevated position minimizes the required hull air gap when drilling over a platform. The X-Y cantilever reach is 100 × 65 ft (30.5 x 20 m).
GustoMSC’s latest iteration of the CJ series is its CJ80-X175-A unit (Fig. 2), developed, the company says, as a result of interest from its customers for a deepwater, robust jackup for Norwegian and UK waters. The hull measures 328 × 360 ft (100 × 110 m), with 761-ft-long legs on 262-ft centers.. The design will have a variable deck load capacity of up to 12,000 tons. None of the CJ80 class jackups has yet to be ordered.
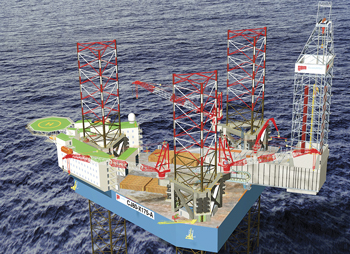 |
Fig. 2. GustoMSC’s CJ80-X175-A design is rated to drill in 575 ft (175 m) of water. |
|
Emphasis of the design is aimed at supporting subsea operations for installing subsea Christmas trees, templates, etc. It will have accommodations for up to 150 people. This design also features its X-Y cantilever, with a capacity of 1,500 tons over a 100- × 80-ft reach. The load can be increased to 2,250 tons over an 80- × 80-ft reach. The CJ80 will be equipped to drill with a subsea BOP and marine riser, rather than a surface BOP found on most jackups.
The unit would be equipped with four 2,500-kW and two 1,750-kW generator sets in two engine rooms, resulting in better electrical load sharing and a reduction of CO2 and nitrous oxide, according to the company. The rig will have offline stand building capability, four mud pumps, and a separate oil-base and water-base mud supply and return system.
BULLY DRILLSHIPS WITH HUISMAN DRILLING TOWER
In 2007, Frontier Drilling awarded a contract to GustoMSC for a custom iteration of its PRD12000 drillship, calling for the designer to shrink the vessel to about 650 ft in length. The result was the PRD12000 Qdrill compact class drillship. This design became known as the Bully rig (Fig. 3). Huisman was contracted for the design and manufacture of the rig’s drilling tower and related pipe, riser and blowout preventer (BOP) handling equipment for Frontier’s Bully I. The modifications were made especially for Frontier Drilling to utilize Huisman’s drilling tower concept that includes pipe and blowout preventer handling equipment. It was the drilling tower design that allowed GustoMSC to shrink the drillships’ size. The rigs’ box-type drilling tower allows offline stand building, with over 43,000 ft of drillpipe and casing racked back in two carousel-type setbacks. Drillpipe and casing are handled in 135-ft lengths. The 2,400 kips drill tower is fitted with active heave-compensated drawworks mounted inside the tower.
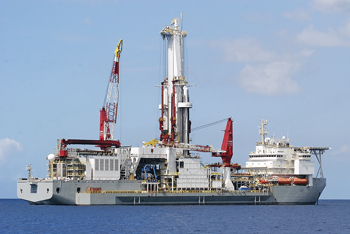 |
Fig. 3. The Noble Bully I, a compact drillship at about 650 ft long, can drill in up to 10,000 ft of water. Use of Huisman’s drilling tower enabled the rig to be shortened, compared with recent “full-size” drillships that can be 750 ft long. |
|
The Bully designs, and Huisman’s Globetrotter design drillships (Fig. 4), are each significantly shorter than 700 ft in length. The Globetrotter drillships are 620 ft long, while the Bully I rigs are about 650 ft in length. For comparison, Maersk Drilling ordered four drillships for delivery in 2013 and 2014 that are about 750 ft long.
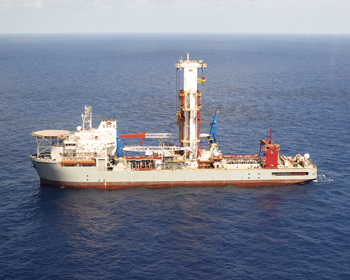 |
Fig. 4. Unlike the Noble Bully series, the Globetrotter drillship is a Huisman design, all around. |
|
Frontier ordered a second Bully rig in 2008. In 2010, Noble Drilling acquired Frontier Drilling, and its Bully I and II rigs under construction.
The drilling tower results in a significantly shorter, more compact drillship design than a “typical” deepwater drillship, which can be over 700 ft in length, primarily to store drill pipe, riser, and other tubulars and equipment for drilling deep wells in deep water. Many of the larger drillships are designed to drill in up to 12,000 ft of water. The Bully and Globetrotter designs also are rated to drill in 10,000 ft and 12,000 ft of water, respectively.
Unlike the Bully rigs, which mated the Gusto-designed vessel with the Huisman-designed drilling tower, the Globetrotter was a Huisman design all around, and is based on the HuisDrill 12000 design. The drilling equipment is based on the drilling tower and pipe storage in carousels installed on the Noble Bully vessels. By fully integrating the designs of the equipment and vessel, its displacement is only 54,000 mt, with operational capabilities equal to units with a displacement of 100,000 mt, the company said. It is suitable for marine drilling riser and pressure riser drilling in unrestricted waters.
The Globetrotter rigs are designed for drilling in up to 12,000 ft of water, have a 2,400 kips static hook load capacity at both the fore and aft side of the mast, and storage capacity for 43,000 ft of pipe.
The Globetrotter’s hull design is as unconventional as the drilling tower. The engine room is placed forward, below the accommodations, which frees the entire aft ship for drilling equipment or tubular storage. All risers, and most of the drill pipe, are stored below deck, aft of the drilling mast. The holds are covered by hatches, leaving a large 45,000-sq-ft free deck area, which can be used for non-permanent equipment. The variable deck load is 20,000 tons.
The dual, multi-purpose drill tower includes two 2.4-million-lb hoists, one above the well center in the drill floor on the forward side of the tower, and the other located above the center in the construction floor on the aft side of the tower. The construction side is used for running the BOP risers, which can be performed during drilling of the surface hole. Stands built on the construction side can be set back in one of the two setback drums located on both sides of the tower. The stands can be taken out of the setback drum and used on the drilling side when ready. Four pipe rackers are mounted on the corners of the tower for handling the stands.
The drill floor is about 16 ft above main deck, which reduces sideways motions at the drill floor and lowers the center of gravity of the drilling equipment. This is made possible by lowering the BOP through a large hatch, aft of the drill mast before skidding it to the well center, forward of the mast. Additionally, the top section of the mast can be removed to allow passage through the Panama and Suez Canals.
ROTATING CANTILEVER FOR JACKUPS
Drilling derricks on jackups typically are moved between wells by skidding sideways over the cantilever, or by sideways skidding of the entire cantilever over the deck box. Huisman’s rotating cantilever concept (Fig. 5) rotates around a fixed point on the deck box and is combined with its multi-purpose drilling tower, instead of a conventional derrick. This combination, according to the company, creates a light construction, allowing a larger drilling envelope at the same leg reactions, providing more free deck space, and a simple deck interface. No flexible connections are required, due to less-complicated interface between the cantilever and the drill floor. Efficiency and safety also are enhanced by integrating the drill floor to the cantilever top deck.
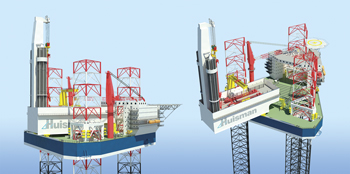 |
Fig. 5. Huisman’s rotating cantilever concept (left) rotates around a fixed point on the deck box and is combined with its multi-purpose drilling tower, instead of a conventional derrick. By rotating the cantilever (right), as opposed to skidding it transversely, the result is a large drilling envelope without sacrificing deck space. |
|
By rotating the cantilever, as opposed to skidding it transversely, the cantilever has a large drilling envelope without sacrificing deck space. It also eliminates the need for a transverse skidding substructure on top of the cantilever, allowing a completely flush deck. The large moonpool area allows for the use of large BOPs. It also provides room to accommodate a subsea Christmas tree.
Coiled tubing and wireline operations are conducted through a second moonpool in the moonpool area, allowing offline workover operations. The rig has 2 × 1,000 kips setbacks and double mouse hole arrangements for offline stand building capabilities. A gantry crane is used for all pipe handling, covering the entire cantilever deck area, including the well center.
The cantilever is 212. 6 ft × 63 ft × 39.4 ft. The cantilever has a maximum reach of 88 ft and can rotate transversely 124 ft. The drilling tower is 200 ft high and features a 2,400-kip hookload, with a 35,000 ft drilling depth.
ULTRA-DEEPWATER CYLINDRICAL SEMISUBMERSIBLES
Sevan Drilling’s ultra-deepwater semisubmersibles are based on the firm’s unique, patented cylindrical hull design. The contractor has one unit in operation, the Sevan Driller (Fig. 6), and two additional units under construction at COSCO in China, for delivery in late 2013 and early 2014. In addition, the cylindrical design also is used as a floating production, storage and offloading (FPSO) vessel.
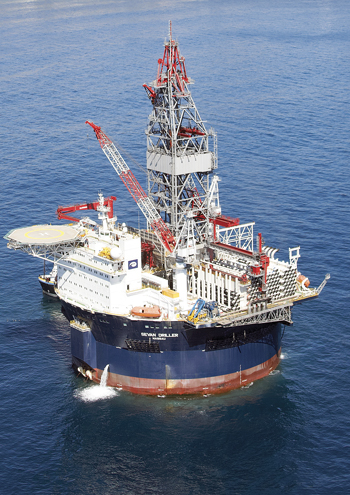 |
Fig. 6. Sevan Drilling’s ultra-deepwater semisubmersibles are based on its unique, patented cylindrical hull design. The contractor has one unit in operation, the Sevan Driller, and two additional units are under construction at COSCO in China for delivery in late 2013 and early 2014. |
|
The main component of the drilling units and FPSOs is the cylindrical hull. The FPSOs utilize the hull for cargo storage and segregated ballast tanks, as well as for marine and utility systems, while the drilling rigs have mud and drill water storage in the hull, as well as cargo and ballast tanks. Pumps and other utility systems related both to the drilling equipment and to the marine systems are inside the hull. The hull is suitable for operation in water depths ranging from 100 ft to more than 10,000 ft and can operate in benign and harsh environments. Station-keeping is provided by a DP3 system, with conventional mooring available for shallow water.
The rig is rated to drill in up to 12,000 ft of water, but the Sevan Driller is equipped for 10,000-ft water depths. The rig can drill 40,000-ft wells. The rig design uses the upper portion of the main hull as a part of the topside structure, accommodating the main power generation plants, mud handling systems, derrick and drilling equipment, and storage for risers, drillstring, casing, and other tubulars and equipment. The accommodations are in the “bow” section of the unit. Drilling operations take place through the center moonpool, which protects the drilling riser and related equipment, as well as protecting the drilling operation in icy areas.
The Sevan Voyageur FPSO (Fig. 7) has all the facilities related to accommodation, utility systems and the process plant on a process deck, which is elevated above the main deck. The topside process systems are separated from the living quarters and utility areas by the provision of a blast-and-fire wall. Facilities for treating and stabilizing the incoming oil and gas are located on an elevated deck. The process systems are modularized and may be fabricated at different yards, and transported and lifted onboard the hull for integration and completion. The hull, accommodation, utility systems and process plant are integrated only to a limited extent, so the construction, hook-up and commissioning could be completed within a short timeframe.
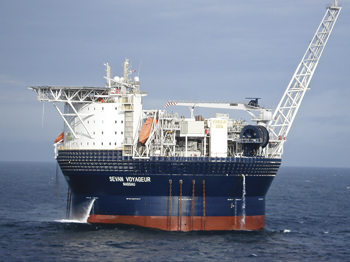 |
Fig. 7. The Sevan Voyageur FPSO, based on the company’s cylindrical semisubmersible design, is contracted to E.On Ruhrgas UK E&P to work in Huntington field in the UK North Sea, in about 400 ft (120 m) of water. It previously worked in Shelley field before undergoing modifications for its present contract. The FPSO has crude storage capacity of 270,000 bbl and can produce up to 30,000 bopd. |
|
The cylindrical hull shape makes the vessels’ responses independent of wind, waves and current headings. Optimum heading can be selected, based on on-going operations. Conditions with wind-driven waves and swell from different directions will not affect the operation, due to the very low pitch and roll motions of the vessel. The rig has a variable deckload of 20,000 metric tons, and with tank capacities, this significantly reduces the need for re-supply and also cuts logistical costs.
The symmetry of the design and the simplicity of the structural arrangement make the hull construction simple and efficient. As a result, no special facilities or infrastructure are required, thus standard shipyard facilities existing worldwide are sufficient to construct the units. 
|