HP/HT Drilling Fluid Additive
Synthetic polymer extends fluid loss control to HP/HT environments
Field experience in Croatia shows that water-based muds formulated with a co-polymer additive enable drilling in HP/HT conditions without formation damage or other problems, eliminating expensive well stimulations.
Karl Heinz Heier, Group Leader, Exploration Chemicals, Clariant Oil Services, Frankfurt-Höchst, Germany, and Brian Lambert, Global Marketing Manager, Clariant Oil Services, The Woodlands, Texas
Drilling muds serve many wellsite functions. They must cool and lubricate the drilling bit, carry rock cuttings to the surface, prevent well collapse by maintaining hydrostatic pressure, and stabilize shales encountered downhole. Water-based drilling muds are increasingly popular. They have a better environmental profile than oil-based muds and generally cost less than invert-emulsion muds.
Fluid loss additives are polymers added to water-based muds to minimize loss of aqueous fluid base into rock, which would cause unwanted increases in fluid viscosity. At low-to-medium temperatures (up to 150°C), starches, starch derivatives and cellulose derivatives provide fluid loss control. However, above 150°C, all polysaccharide-based polymers can be degraded thermally or by oxidation.
Thus, the increasing need to drill in more aggressive environments prompted Clariant Oil Services to develop fully synthetic polymers that could be effective fluid loss additives in water-based muds at high temperatures and pressures.
PRODUCT DEVELOPMENT
The latest generation of fluid loss additives, represented by Hostadrill 4706, is based on vinylsulphonate and vinylamide chemistry, and extends temperature stability up to 230°C, while offering a high tolerance to electrolytes and improved rheological properties.
Hostadrill 4706 is a co-polymer with a molecular weight of 0.5-1 million Daltons, Fig. 1. During product development, more than 1,000 polymer variants were tested in the company’s R&D laboratories in Frankfurt-Höchst, Germany. Development tests were conducted to international (e.g. API) standards, or to even stricter client standards. For final product definition, reproducibility was ensured by only using samples from a pilot plant or full-scale manufacturing batches.
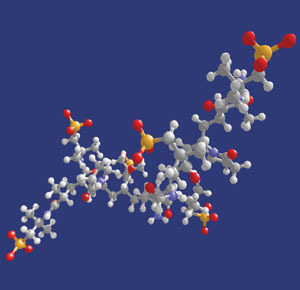 |
Fig. 1.A section (molecular weight 2,000) of the Hostadrill 4706 co-polymer molecule.
|
|
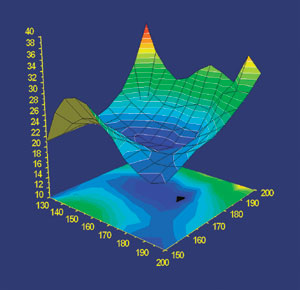 |
Fig. 2.Hostadrill 4706 fluid loss behavior, with 15-hr aging in a saturated sodium chloride clay-based mud at various temperatures and molecular weights (k-values). The test shows that under these conditions, the optimum k value lies between 155 and 185.
|
|
The product was tested in various mud formulations, many sourced directly from the field. In terms of fluid-loss behavior and temperature stability, the optimized product was a significant improvement on earlier developments. In addition, its tolerance of highly concentrated brines (up to saturation) and divalent cations (calcium, magnesium), showed a distinct advantage over polyacrylamide chemistry. The molecule can also be degraded by oxidation, leaving no insoluble degradation products.
FIELD APPLICATION
While working with Croatia’s INA Naftaplin, M-I Drilling Fluids found an ideal, early application for the new polymer. The challenge was to formulate a mud system that would be effective in high-pressure/ high-temperature (HP/HT) gas wells, in an area where oil-based and invert-emulsion fluids were prohibited.
Five gas wells, in Kalinovac and Molve fields, exhibited pressures of more than 400 bar and static bottomhole temperatures (BHTs) within the 180 – 200°C range. Four wells were deviated slimhole re-entries, drilled to between 3,400 and 3,750 m (11,155 and 12,303 ft) at angles of 0° to 40°. The drilling fluid had to fulfill many criteria, such as remaining stable for more than 100 hr at BHT without circulation, while tool changes or logging operations took place. Due to the high cost of drilling slimhole HP/HT wells, minimization of lost time, due to hole or fluid instability, was critical.
The fluids firm conducted laboratory tests with a number of mud formulations to attain the required properties. The first well was drilled with a mud that contained the co-polymer and bentonite to support the polymer’s fluid loss properties and act as a viscosifier. Although final well depth was reached without problems, it was found through hydrodynamic measurements (yielding a skin factor of 22.9) that the formation had been severely damaged, due to the presence of bentonite. Thus, it was necessary to conduct a near-wellbore stimulation procedure before reactivating the well.
M-I conducted further lab tests to develop a mud that could achieve the required properties in the absence of bentonite. Accordingly, xanthan gum and an acrylamide co-polymer were included to provide suspension and carrying properties. The co-polymer and resinated lignite were used in combination to limit fluid loss.
Although there were concerns regarding the xanthan gum’s thermal stability, it was assisted by the co-polymer and other components in the mud formulation. As regards the second well, the fluid proved to be stable, even during a 56-hr period at bottomhole conditions without circulation. No formation damage occurred, and no stimulation was needed.
A similar mud formulation was used for the remaining three wells, except that the co-polymer concentration was increased, while the resinated lignite concentration was reduced by up to 50%. No fluid-related problems arose, and the wells were drilled without formation damage (shown by hydrodynamic measurements). No stimulation was needed.
Thus, the use of the Hostadrill polymer with xanthan gum in the field development program minimized formation damage and resulted in a gas production increase of 151% to 279%.
CONCLUSIONS
Usage of water-based drilling fluids under hostile (HP/HT) conditions is increasingly common, where invert-emulsion muds would normally be used, but are prohibited due to environmental considerations. A newly-developed fluid loss additive, based on a synthetic, vinylsulphonate/ vinylamide co-polymer, offers stability at temperatures up to 230°C and in high-salinity brines.
Field applications showed that muds fomulated with the polymer enable HP/HT drilling. There has been good fluid loss control, with no fluid-related problems. Thus, HP/HT wells can be drilled without damaging the formation, reducing operating costs, as expensive well stimulations are eliminated. 
ACKNOWLEDGMENT
The authors thank the management of Clariant Oil Services, M-I Drilling Fluids and INA Naftaplin for permission to publish this article. They also acknowledge the contributions of Tomislav Soric´ (INA Naftaplin), Robert Huelke and Pavel Marinescu (M-I Drilling Fluids) in sharing field application experience.
THE AUTHORS
|
|
Karl Heinz Heir is group leader, Exploration Chemicals, for Clariant Oil Services in Frankfurt-Höchst, Germany. Since 1998, he has been responsible for R&D, mainly in application of water-soluble polymers and surfactants/ corrosion inhibitors in exploration. Formerly, Mr. Heier worked within Clariant and Hoechst AG on applications for construction, metalworking and petrochemicals. Before joining Hoechst AG in 1975, he received the degrees of Diplom Chemist and Dr. rer nat at the Universities of Würzburg and Regensburg, Germany.
|
|
Brian Lambert is global marketing manager for Clariant Oil Services, based in The Woodlands, Texas. He manages the company’s relationships with key global customers, and the group’s product marketing strategy and communications. Prior to moving to Houston in 2003, Brian spent 14 years in the Far East, where he was regional manager. He earned a BSc degree in chemistry with biochemistry from the University of Leicester, UK, and an MBA with distinction from the University of Hull, UK.
|
|
|
|