Coalbed Methane Report
Accurate gas content analysis improves coalbed gas resource estimation
Careful acquisition, handling and analysis of coal samples in the field and in the laboratory help pin down elusive “lost gas” for resource calculations.
Noel B. Waechter and George L. Hampton III, Hampton, Waechter & Associates, LLC, Englewood, Colorado; Stephen D. Schwochow, Geological Consultant, Golden, Colorado; and John P. Seidle, Sproule Associates, Inc., Denver, Colorado
For the natural gas industry, the direct and accurate measurement of gas content in coal is a critical step toward estimating the in-place gas resource potential of coals. Without proper sample selection and handling procedures, the validity and usefulness of gas-content data can be compromised. Here is what a resource assessor needs to know.
GAS CONTENT DETERMINATION
Early attempts to devise a standardized methodology for analyzing the gas content of coal were aimed at evaluating and mitigating methane-emission hazards, which have plagued underground coal mines for centuries. Developed first in France in 1970 and subsequently refined by the late US Bureau of Mines, what has evolved as the “Direct Method” forms the basis of most techniques used today in the natural gas industry to estimate subsurface gas content and gas production potential of coals and organic shales.
Gas content is not a singular entity but an intimate combination of three distinct components. First is “sorbed” gas, the volume of gas that desorbs from the coal matrix and that can be measured directly and relatively simply. According to the Direct Method, sorbed gas is quantified by recovering a core sample from a wellbore, sealing it as quickly as possible inside an airtight canister, and then periodically measuring the volumes of gas released inside the canister at atmospheric pressure, Fig. 1. Gas-volume measurements typically are plotted against the square root of time, as shown in Fig. 2. Full desorption may require two months or longer to complete. For practical purposes, the effective end of the desorption cycle is the time at which the cumulative desorption-volume curve flattens to near-horizontal.
 |
Fig. 1. Typical gas desorption canister, barometer and burette. Burette size varies according to expected gas volumes.
|
|
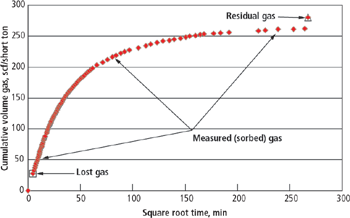 |
Fig. 2. Typical plot of desorbed gas volumes vs. square root of time.
|
|
Second, “lost gas,” the most problematic component to ascertain, is the volume of gas that unavoidably escapes to the atmosphere and the wellbore between the time the coal sample is retrieved (cut) in the wellbore and the time at which it is sealed inside the desorption canister. It is estimated by mathematically extrapolating the first few hours of desorbed volume-vs.-time measurements to “time zero.” By convention, time zero is taken as the estimated time at which the sample was halfway out of the wellbore for water-filled drill holes. For air- or mist-drilled wells, time zero is the estimated time at which the sample was cut.
The third component, “residual gas,” is the measurable volume of gas remaining in the sample after desorbed volumes have diminished to some low, arbitrarily defined level, Fig. 2. This is measured by pulverizing the sample in an airtight ball mill or rock crusher at the end of the desorption cycle.
In the following discussion, we will examine how later refinements to the Bureau of Mines' Direct Method, as well as other new procedures developed in the field and in the laboratory, have greatly improved the accuracy of our gas-content calculations.
FIELD PROCEDURES
Sampling procedures and sample handling are critical factors in determining each gas component, especially lost gas. To improve the accuracy of sorbed-gas and lost-gas calculations, we recommend the following:
- Use coring methods designed to maximize core recovery, minimize uphole travel time, and minimize surface core handling, preparation and placement inside the canisters under given field conditions.
- Maintain canisters at reservoir temperature.
- Record canister temperature, barometric pressure and time for all desorption readings.
- Normalize gas volumes to standard temperature and pressure.
- Correct readings for changes in headspace volume.
- Estimate lost-gas volume using the proper curve to fit the data.
To satisfy these criteria, certain logistical arrangements must be made at the wellsite. First, a temperature-controlled trailer with a reliable source of power and clean water is necessary to serve as an onsite field laboratory.
After a core has been retrieved, it is removed from the inner core sleeve and laid out on a catwalk or, preferably, in a core-handling trailer. If gassy coals or shales are present in the core, brief field descriptions should be recorded quickly. With depth intervals marked, the cores are sealed inside the desorption canisters. Minimize potential oxidation and desiccation of low-rank coals by filling the canisters with water or inert gas where appropriate.
It has been demonstrated that desorbing gas from samples kept at reservoir temperature more realistically reflects the subsurface conditions under which the gas would actually desorb when it is produced. In the field laboratory trailer, the canisters can be heated to, and maintained at, reservoir temperature (log recorded) by means of thermostatically controlled water baths, air boxes or thermal blankets. Water baths afford the best heat conduction.
If the coals appear very gassy, readings should commence as soon as possible and should include time and date, canister temperature, air temperature and barometric pressure. These data will be used to reduce gas volumes to STP and to make volumetric corrections for expansion or contraction of the headspace (the space between the sample and the canister wall/lid). Time intervals between readings will vary depending on gas content and diffusivity. Readings should be taken at the wellsite for at least 24 hours if possible. The canisters can then be transported to a central offsite laboratory where they are reheated and readings resumed.
ESTIMATION OF LOST GAS
The accuracy of lost-gas determination is improved by using a coring method designed to deliver the coal sample from the formation to the canister as quickly as possible, by maintaining canisters at constant reservoir temperature, and by extrapolating lost-gas volume to time zero using the proper curve to fit the data.
The convention of selecting time zero, as noted earlier, is based on the premise that, although desorption starts as soon as the sample reaches the depth where hydrostatic pressure is less than reservoir pressure, desorption proceeds at a slower rate than when the confining pressure on the sample is atmospheric, which is the pressure at which desorption readings are taken. In reality, desorption of gas occurs at variable rates during the trip uphole, and modeling the actual behavior is difficult if not impossible. So, choosing the halfway mark is simply an approximation that most contractors use.
When drilling with mud, one must consider the mud weight and whether the hole was drilled balanced or overbalanced. If drilled overbalanced, time-out-of-the-hole starts when the sample reaches a depth where hydrostatic pressure in the hole equals the reservoir pressure.
Diffusion models suggest that the percentage of gas desorbed (or cumulative volume) varies linearly with square root of time for the initial 20% of desorbable gas, assuming spherical coal particles. As the Direct Method was applied to deeper wells, the 20% limit came to mean “early in desorption.” So, the typical graphical solution for lost gas was to extrapolate the first several hours of readings to time zero using a linear fit to the plot of cumulative gas vs. square root of time.
As an example of such a projection, let us look at an Upper Cretaceous Rocky Mountain coal containing 280 scf/short ton of total gas. In Fig. 3a, the linear fit to 2.8 hours of readings matched the data closely and yielded a lost-gas value (y-intercept) of 1,646 cc. With additional readings (6.8 hours), the linear fit is not as close, and lost gas drops to 1,469 cc, Fig. 3b. When a polynomial equation is fitted to the longer data set, the correlation is better and yields the highest lost-gas volume, 1,886 cc, Fig. 3c.
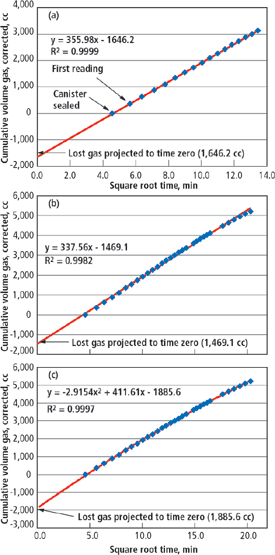 |
Fig. 3. Example of variation in lost-gas extrapolation. (a) Linear fit to 2.6 hours of readings. (b) Linear fit to 6.5 hours of readings. (c) Polynomial fit to 6.5 hours of readings.
|
|
These differences become more pronounced in coals with high diffusion rates and high gas contents. Fig. 4 compares linear and polynomial fits for a different Cretaceous coal that contains 630 scf/short ton of total gas. Even though the total reading time, 4.4 hours, was shorter than in the first example, the high gas content and high diffusivity of this coal yield a cumulative desorption curve that is obviously nonlinear. With a polynomial fit (solid line), lost gas is estimated at 23,824 cc, whereas the linear fit (dashed line) gives only 10,289 cc.
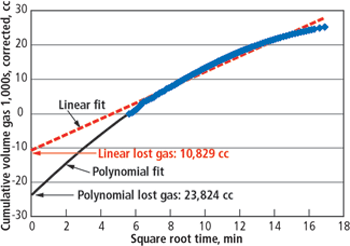 |
Fig. 4. Comparison of linear and polynomial fits in a coal with high gas content and high diffusion rate after 4.2 hours of readings.
|
|
Using linear fits for lost gas has been the industry standard for years. Since 1999, Hampton, Waechter & Associates, LLC has used both polynomial fits and linear fits and, with few exceptions, we have found that polynomial fits extrapolate to the target more consistently than do linear fits. As lost-gas time increases, the linear fit progressively underestimates lost-gas volume. In other words, because of the longer uphole trip time, more gas is lost initially, and early-time desorbed volumes therefore are less, which imparts a lower slope to the desorption curve, whose early-time tangent (that is, the linear fit) intercepts the y-axis higher (closer to zero) than it should.
Also, it is within the first two hours of desorption readings that the data used to extrapolate lost gas are the least stable because the enclosed core often has not yet been fully heated to reservoir temperature. As the core's temperature rises, the rate of gas diffusion increases, often resulting in a linear or even concave-up desorption curve. This effect is most pronounced when reservoir temperatures are high and surface temperatures are very low (that is, in winter). For a polynomial fit, four to five hours of desorption readings can be used for extrapolating the lost-gas curve, if gas volumes are great enough. With a larger number of data points, the curve is more influenced by the data collected after the core's temperature has stabilized.
LABORATORY PROCEDURES
After the canisters are returned to the laboratory, they are reheated to reservoir temperature, and readings are continued. For coals of high gas content, readings may be necessary several times a day during the first few days, but then their frequency can be decreased as the rate of gas desorption decreases. Gas sampling should be continued throughout in order to monitor sequential compositional changes with time. If desorption volumes are sufficient, at least three gas samples – early, middle and late – should be taken from each individual bed or zone. These analyses help determine heat content and gas quality for pipeline requirements.
Desorption should continue until the readings approach some insignificant level. When to terminate desorption can be based on an arbitrary desorption-rate cutoff, for example, 0.05 cc/g/d over a one-week period, or when the cumulative desorption curve has flattened, Fig. 5. Alternatively, the sample may be crushed early to expedite the desorption cycle.
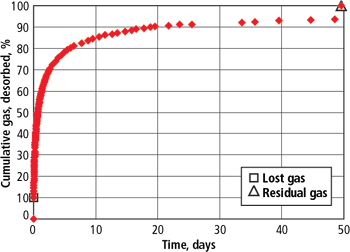 |
Fig. 5. Cumulative percentage of gas desorbed vs. time, illustrating the effective end of desorption cycle.
|
|
Upon completion of desorption, canister headspace is measured, and the samples are reweighed and split into fractions. Measurement of residual gas should then begin immediately, even if the samples are no longer releasing gas. (Removing the sample from the 100%-methane atmosphere of the canister accelerates the loss of any remaining gas.) Residual-gas measurements should be made at reservoir temperature using inert gas to minimize adsorption of air and oxidation of the sample. Although not produced from the reservoir, residual gas is still part of the total gas measured on the adsorption isotherm and therefore must be included in the calculations.
Two additional useful analyses can be performed on duplicate samples or splits of the desorption samples. Proximate analyses (for moisture, ash, volatile matter, fixed carbon, sulfur and heat content) enable gas contents to be expressed on dry ash-free and dry mineral-matter-free bases. Adsorption isotherms (also known as sorption isotherms) of representative samples are used to determine the degree of gas saturation. When a mixture of gases is present, a separate isotherm of each gas species is necessary to realistically model the adsorptive capacity of a given coal.
Other analytical procedures and data that a client might request include bulk-density measurement, gas isotopic composition, petrographic description, slabbing and photography, coal maceral composition, cleat geometry and mineralogy, vitrinite reflectance, pyrolysis and, for mixtures of coal and carbonaceous shale, total organic carbon (TOC).
SELECTING THE BEST SAMPLE
How downhole samples are collected for desorption has an enormous impact on the reliability of gas-content data. A procedure that recovers a large, relatively unbroken sample of coal and brings it to the surface in the least amount of time yields the best results.
Continuous wireline core-retrieval systems fulfill these requirements well. Wireline rigs recover core continuously in multiple runs and typically can core 100 to 300 ft within a 24-hour period, usually with better recovery than conventional coring. This is particularly advantageous when coring highly fractured coals or multiple coal seams distributed over a wide stratigraphic interval.
In a 2,000-ft hole, for example, wireline core retrieval takes about six to eight minutes, compared to two or three hours for a conventional coring rig. In addition, with wireline systems, core starting points can be selected to allow for a greater margin of error.
Wireline systems can be costly because they require either a special coring rig or modifications to an existing drill rig. If only one or two seams are to be cored and if drilling depths are not great, conventional coring can provide gas-content data as reliably and at less cost; however, uphole trip times are longer.
When conventional coring is impractical, rotary sidewall coring can be an acceptable alternative. Although sidewall cores are small and many samples must be taken for adequate statistical accuracy, retrieval times are relatively short. Bulk density, gamma ray and caliper logs are used to pick the core points. Inasmuch as washouts and filter-cake buildup can inhibit sidewall core recovery, close attention must be paid to the caliper log.
Furthermore, logging delays or other problems that cause the wellbore to remain open for extended periods can lead to excess gas depletion from the coal prior to sampling, thereby skewing gas-content results. But under optimal borehole conditions, gas contents derived from rotary sidewall cores can be as accurate as those derived via a wireline coring rig, Fig. 6. Miniature desorption canisters have been designed specifically for sidewall core analysis.
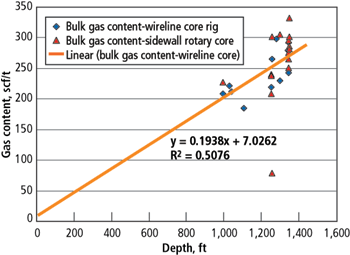 |
Fig. 6. Comparison of desorbed gas contents of wireline whole core and rotary sidewall cores taken from the same wellbore over the same intervals. Example of Cretaceous coal from the Greater Green River Basin, Wyoming. Courtesy of Steve Hollis, Double Eagle Petroleum
|
|
Percussion sidewall cores are not recommended because they damage the coal integrity and allow gas to escape too quickly.
Desorption of drill cuttings provides a quick look at gas content in exploratory situations when coring is impossible or impractical. Analyses of infill well cuttings are also useful as a supplement to core data.
Although gas-content values determined from cuttings generally are not that reliable, we have observed mixed results. In some cases, the dry ash-free gas contents of cuttings from reamed core intervals were nearly identical to those of the cores. In other instances, estimated gas content was only half that for core from the same interval as a result of the small cuttings particle size, which allowed gas to escape more quickly.
The Smith and Williams Method was developed specifically to improve the accuracy of lost-gas estimation from cuttings, but the technique is cumbersome and does not conclusively improve results.
HOW COALBED GAS RESOURCES ARE CALCULATED
Estimation of coalbed gas resources follows a straightforward equation that yields original gas-in-place, Gi (in Bcf), also known as GIP:
where A is drainage area or drillable area (acres), h is coal seam thickness or net thickness (ft),rb is average bulk density (g/cc) and Vi is the mass average gas content (scf/short ton) obtained from desorption tests.
Obviously, the accuracy of GIP is directly and cumulatively affected by the accuracy of each variable. We have seen how sample type and lost-gas determination affect total gas content. The remaining terms also have limitations that warrant some cautionary remarks.
Area usually can be accurately quantified – a lease block of specified acreage or the planimetric area of a coal field delineated by the present limits (surface and subsurface) of the coal-bearing formation(s) under consideration.
Net coal thickness refers to the cumulative thickness of as many coal seams as may be assessed within a stratigraphic interval. Seam thickness data may come from direct measurements on outcrops or in mines, but these cannot reliably be projected very far into the subsurface. Coal exploration boreholes yield accurate thicknesses but only to depths of prospective mining.
In the absence of cores, the next best subsurface measurement of coal thickness comes from geophysical logs. Although the combination of resistivity and SP is useful, the most versatile suite is the density log, which includes bulk density, gamma ray, caliper and photoelectron curves. Note, however, that identifying coals and measuring their net thickness on the bulk density curve depends on the maximum or cutoff value assumed for coal density. Sonic logs are especially valuable in deeper boreholes because the sonic response is less adversely affected by coal washouts than is density.
Coal densities vary according to rank because rank progression or maturation entails changes in coal's molecular and physical structure. The US Geological Survey uses the following average values in its calculation of coal resources: anthracite and semianthracite, 1.47 (g/cc), bituminous, 1.32; subbituminous, 1.30; lignite, 1.29. Other reported values in use can vary 25% to 100% within any rank category.
Higher densities may be warranted based on ash content of the coal. Many investigators use a cutoff of 1.75 g/cc when picking coalbeds on density logs. Hampton, Waechter & Associates, LLC uses values of 1.75 to 2.0 depending on the coal characteristics of a particular basin.
The variables Ahrb in the equation constitute the coal resource. For preliminary fieldwide assessments, be aware of three limitations when using published coal resource estimates. First, they usually include only selected minable coal seams, not necessarily all potentially gas-bearing seams. Second, they may or may not have excluded mined-out areas. Third, assessments commonly extend only to a maximum underground minable depth, usually 3,000 ft. We now know that, in some cases, such as in White River Dome field in Colorado's Piceance basin, coal seams can yield commercial quantities of gas from depths of 8,000 ft.
Where only extremely few gas-content data are available, or none at all, one may have to resort to empirical approaches that statistically relate gas content with depth and/or coal rank, or empirically based information on known gas contents in a geological setting of similar coal age, rank and depth. While not accurate, such approaches may be valid when deriving a “first-look” indication of gas potential, such as in a virgin coal field. Be cautious of cited GIP estimates for which the basis of the derivation cannot be ascertained, especially those that might appear in promotional literature or prospect documentation.
RESOURCES TO RESERVES
Desorption test results are employed in a variety of reservoir engineering tasks that help determine reservoir producibility and ultimate recovery. The degree of gas undersaturation, for example, is calculated from these tests, together with the sorption isotherm and initial reservoir pressure. Reservoir simulation models, whether simple, single-well models or full-field studies, must be initialized with various parameters, including gas content. Combining desorption test results with the sorption isotherm allows production engineers to better understand well behavior throughout the course of depletion and to estimate recovery factors.
The recovery factor is essential in bridging the gap between resources and reserves. Note that the calculated GIP is the theoretical in-place resource, as opposed to the recoverable gas resource or gas reserves. Generally speaking, desorption test results allow a property to be classified as possible resources. Moving from possible to probable resources (the most assured category of potentially recoverable resource, as defined by the Potential Gas Committee) and then, ultimately, to proved reserves requires knowledge of such additional factors as gas producibility and commercial viability of a prospect. Reserves in proved undeveloped locations are calculated by combining desorption-based volumetric gas contents with recovery factors.
When evaluating a lease or coal field for gas potential, remember the fundamental limitations and requirements for obtaining the most accurate estimate possible of in-situ gas content. Be prepared to invest the requisite cash and time with a service contractor who has the experience, staff and equipment to properly recover and prepare coal samples and conduct full-cycle desorption analyses under appropriate field and laboratory conditions. 
THE AUTHORS
|
|
Noel B. Waechter has over 30 years' experience in petroleum exploration and development and metals exploration, with diverse expertise in coalbed gas exploration and desorption technology, wellsite geology, petroleum reservoir stratigraphy, seismic interpretation and source-rock geochemistry. He has headed his own consulting firm, N.B. Waechter & Associates, Inc., since 1983, following employment at Amoco Production and other exploration companies. Mr. Waechter received a BA degree in Geology from the University of Montana and an MA in Geology from the University of Texas at Austin. He has published a number of technical papers on petroleum geology and coalbed gas and has presented lectures at various technical and professional meetings.
|
|
George L. Hampton III has been involved in the CBM desorption (gas content) business since 1988, and he formed Hampton, Waechter and Associates in 1998. He is also president and chief geologist of Hampton & Associates, Inc., a consulting company formed in 1986 that specializes in all geologic aspects of coalbed methane exploration, drilling, completion and production. Mr. Hampton has 25 years' petroleum industry experience with 23 years dedicated to CBM. He began his career with Amoco Production Co. (Denver, 1978 – 1986). He received his BS and MS degrees in Geology from Brigham Young University.
|
|
Stephen D. Schwochow is an independent geological consultant and technical editor. He currently researches and reports on US and international CBM developments for industry clients and the Potential Gas Committee. Previously, he served as technical editor of GRI's Quarterly Review of Methane from Coal Seams Technology. As a cofounder of Cairn Point Publishing Inc., he was lead researcher and author of that group's International Coal Seam Gas Report.
|
|
John P. Seidle has more than 20 years' experience in unconventional gas, primarily in coalbed methane. As a senior reservoir engineer with Sproule Associates, Inc., he is involved in the technical and economic aspects of CBM exploration, production and enhanced recovery, and teaches an industry short course on CBM. He received his PhD in Mechanical Engineering from the University of Colorado and is a registered professional engineer in Oklahoma, Colorado and Wyoming. He has authored 19 technical papers and has been awarded six patents.
|
|